To limit global warming, we need both a drastic reduction of carbon emissions and a way to extract and re-use carbon dioxide from the air. Why not tackle both challenges together? The idea behind ‘Power-to-Molecules’ is to decarbonize industries by producing renewable hydrogen in the first stage and converting carbon dioxide to renewable fuels or chemical building blocks in the next stage. To get this done, imec/EnergyVille is working on solutions to make large-scale green hydrogen a reality and to generate hydrocarbons from recycled carbon dioxide.
If we want to limit global warming to two degrees Celsius, the net global CO2 emission must drop to zero by 2050. With the help of solar panels and cars driving on green electricity, carbon emissions can fall rapidly in the transportation and building sectors. However, in other industrial sectors - like the steel or cement industry - such a drastic reduction is far less realistic. The Intergovernmental Panel on Climate Change (IPCC) assumes that emissions in these sectors will not completely disappear and that they can only be offset by the active removal of carbon dioxide from the air.
Based on IPCC predictions, carbon emissions in industry and agriculture will decrease slower than in power and transport.
"There’s a lot of research on carbon capture and storage, but we're already investigating the next step: how can we re-use this carbon? Plants capture CO2 from the air and convert it into hydrocarbons. In fact, we want to do the same, but more efficiently", says Bart Onsia, business development manager at imec/EnergyVille and expert on energy conversion. Within the scope of 'Power-to-Molecules’ (P2M) various new technologies are being explored, each with the idea of converting water and carbon dioxide into valuable substances for industry. Depending on the substance, these processes are also labeled Power-to-Gas or Power-to-Liquids. Bart Onsia: “The molecules in 'Power-to-Molecules' can refer to either a gas or a liquid. These can be fuels such as hydrogen, methanol or ethanol, but also compounds like ethylene or syngas that can be used as basic components for the chemical industry, to make polymers for instance."
This conversion requires energy. “Any electrical energy will do, but if we want to create green chemicals, we better use solar energy (in that case often called 'solar fuels') or wind energy. Green energy can be used whenever it is available, and the P2M-capacity can be used to mediate excess energy,” Bart Onsia explains. Ideally, this should be done close to the source, he says. "Losses are associated with energy transport. Offshore wind farms, for instance, are interested in converting the generated energy directly into hydrogen. Instead of storing the overproduction in a battery, they could store it as a renewable fuel.”
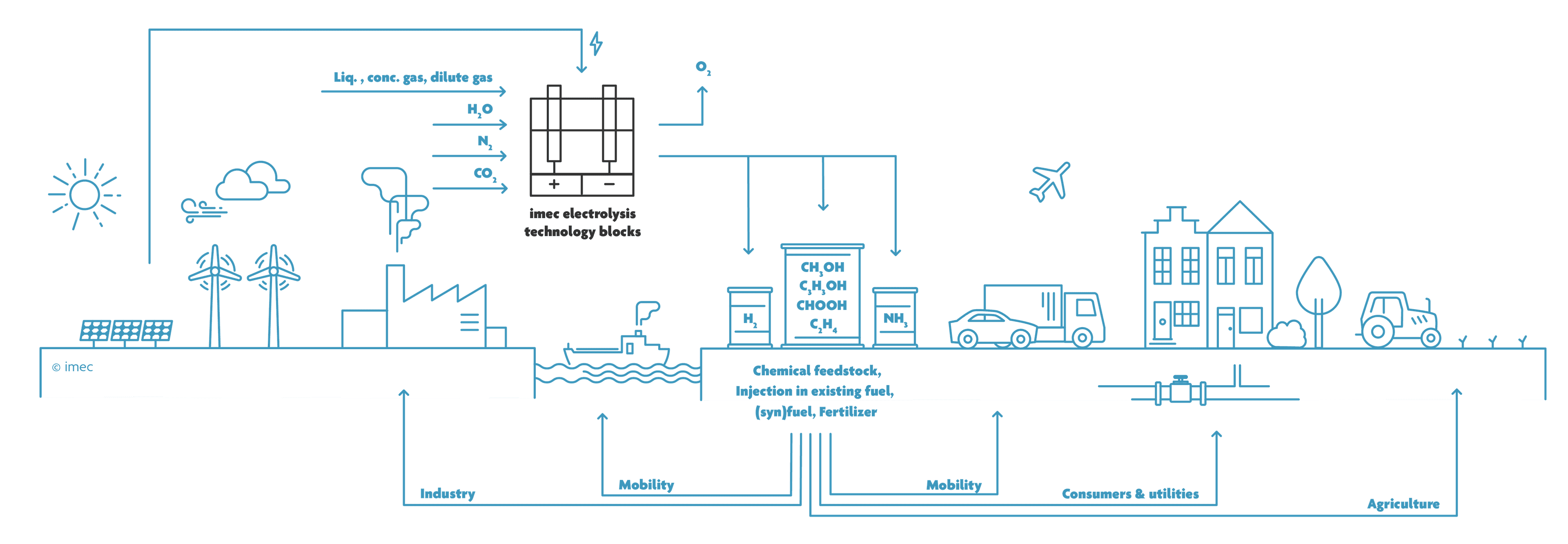
The idea behind Power-to-Molecules: Water, carbon dioxide or nitrogen are converted through renewable energy into chemical compounds that can be useful for the chemical industry, energy or agriculture.
From grey to green hydrogen
If we want to use renewable energy to make useful molecules, hydrogen (H2) is the most obvious candidate. The chemical and steel industries now mainly use 'grey' hydrogen, produced by steam reforming. In this process, natural gas and steam are combined at high temperature. Together with the hydrogen gas, carbon dioxide is formed as side product.
However, a more ecological way of producing hydrogen is by the electrolysis of water. Those of you who remember their high school chemistry experiments know what happens when you dip two electrodes in water and connect them to a power source: bubbles form. Under the influence of electric current, hydrogen gas is created at the negative pole and oxygen gas at the positive pole.
Yet we do not heat our houses with hydrogen and we hardly see hydrogen cars on the road. Electrolysers for industrial applications have been on the market for some time, but their price point is too high to harvest green hydrogen on a large scale. Electrolysis is used for only five percent of global hydrogen production. “With steam reforming you pay about two euros per kilogram of hydrogen. With electrolysis, this cost is currently at least three times higher, depending on the scale,” Bart Onsia says. “This difference is not only explained by the efficiency of the process, because it also depends on the costs of the electricity, the distribution costs and the lack of scale. I am convinced that we can make electrolysers much smaller and more efficient. This will reduce the costs of green hydrogen production, making it competitive with the way hydrogen is produced now.”
How can we make this process more efficient and what technological innovations do we need? There are a couple of options for industrial electrolysers. Let’s have a look at a large-scale, state-of-the-art alkaline electrolyser. A 5MW electrolyser contains about 170 electrolyser cells connected in series and can produce about 100 kilogram of hydrogen per hour. Each electrolyser cell consists of porous metal rings as electrodes, sometimes two meters in diameter. The electrodes in each cell are separated by a diaphragm or separator membrane. This separator passes the ions (OH- and K+ in this case) but stops the gasses from intermixing: you don’t want the produced hydrogen gas and oxygen gas to meet, as this would result in an explosive mixture. The critical reactions in the electrolyser cell take place at the surface of the electrodes, where three different phases - solid, liquid and gas – meet.
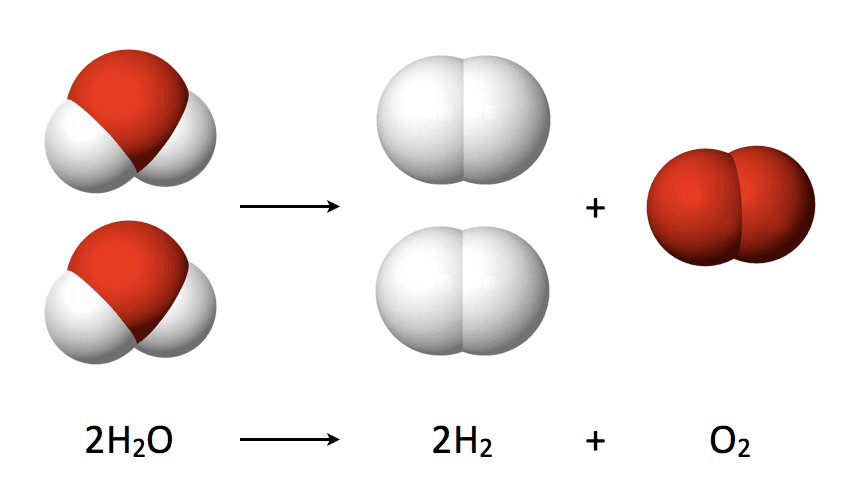
Nanomesh: The area of a soccer field in a soda can
As the efficiency is determined by chemical reactions that take place on a surface, a very large surface area is preferred. Together with KU Leuven, imec has developed a ‘nanomesh’, a material with a very high surface-to-volume ratio. “For each micrometer thickness, there is a 33-fold increase of available surface area”, states Philippe Vereecken, scientific director at imec. “To visualize this: when filling a volume of a small can of soda, it would remain 75 percent empty while containing a surface area equal to the size of a soccer field.”
Besides this large effective surface area, the electrodes also need a porous structure to bring the reactants to the reaction surface and to remove the products that are formed. The nanomesh, which looks like a microscopic 3D chicken wire, combines both properties. “The material is made up of millions of upright nanowires that are horizontally interconnected on multiple levels, showing highly regular internal spacings and dimensions. As a result, it combines an unprecedented surface-to-volume ratio with a high porosity”, says Vereecken. “On top of that, the internal and external dimensions can be tuned to almost any specification, making it potentially compatible with a multitude of application requirements.”
The gas bubbles at the nanomesh (in the middle) show a larger and more continuous hydrogen production compared to a nickel foam (left) and compared to a carbon cloth with platinum (right).
The nanomesh combines a large effective surface area (vertical axis) with a high porosity (horizontal axis). ( Source: Combining High Porosity with High Surface Area in Flexible Interconnected Nanowire Meshes for Hydrogen Generation and Beyond)
Because of the large area enhancement, the electrode can be much thinner. Imec also works on thinner membranes to further reduce the distances between the electrodes and reduce ohmic losses. "The more current sent through an electrolysis cell, the more hydrogen is formed, but also the higher the losses. We can avoid the latter by miniaturizing everything with our nanomesh and membrane technology," says Philippe Vereecken. Finally, efficiency can be further increased by making better coatings for the electrodes. "This involves deposition of thin films of specific materials, a research field in which imec has world-leading expertise. With our microelectronics experience we can provide nanomaterials for upscaled energy devices”. According to Bart Onsia, this will make the large-scale production of green hydrogen possible. “We’ll take this step by step”, he says. "We start off with water-fed cells but will evolve to vapor-fed cells and eventually cells that use the ambient moisture for hydrogen generation.”
The three-stage rocket to a low carbon economy
The electrolysis technology will play a key role in the transition to a low carbon economy in two ways. In the long term, it will help us to convert and re-use carbon dioxide, but in near future, we can also use green hydrogen to reduce carbon emissions in various industries. Electricity, heat or motion can be generated from the energy embedded in the hydrogen molecules. A fuel cell works according to the reverse principle of electrolysis: generating electricity by the conversion of hydrogen and oxygen into water. The hydrogen car might be the best-known application, but it also has the potential to decarbonize heavy duty transportation (e.g. ships and trucks). In addition, hydrogen can also be used as a fuel, without releasing carbon dioxide during combustion.
Stage 1: renewable hydrogen is used to help decarbonize various industries
Bart Onsia sees a direct benefit for the introduction of green hydrogen, particularly in the steel and cement industries. "The population is growing, and we keep on constructing. For buildings we need concrete and steel. According to IPCC predictions, the steel industry will continue to grow by thirty percent until 2050. For every 2.3 metric tons of steel made from coal, one metric ton of CO2 is released. To reduce the iron-ore, we can also use hydrogen, but we need gigantic quantities, about 50 million tons of hydrogen per year. In the cement industry we have a double problem, because carbon dioxide is not only released as a combustion product from the applied heat, but also as a product of the calcination reaction itself. The production of one metric ton of cement from calcium carbonate produces 0.9 metric tons of CO2, one half from the reaction and the other half from the heat. So, there's still a lot of margin for decarbonization in these sectors".
Stage 2: renewable hydrogen is used to convert concentrated, pure CO2 into compounds that are valuable for industry
The large-scale production of green hydrogen will be necessary to break our addiction to fossil fuels, but this is only the first step. In a next phase, the hydrogen will be used in combination with electroreduction of CO2 to make methanol, methane and other products. Initially, concentrated pure CO2 will be used, but at a later stage the carbon dioxide can be captured from factory chimneys. In the long term, dilute carbon dioxide (400ppm) can be captured directly from the air, making a circular CO2 economy possible. "Nowadays, hydrogen is combined with CO2 to form chemical substances in several steps, with each step having a certain efficiency. We have the technology to do everything in one step: a direct and selective conversion of carbon dioxide into substances like methanol, ethanol, formic acid, and others," says Bart Onsia. Another long-term goal of the 'Power-to-Molecules' roadmap is to immediately convert nitrogen from the air into substances that are useful for agriculture. Such methods will be needed to become carbon neutral by 2050. Thorough innovation is crucial for the rapid deployment of this renewable technology and to make the transition to a new energy area.
Stage 3: dilute CO2 is recycled in one step
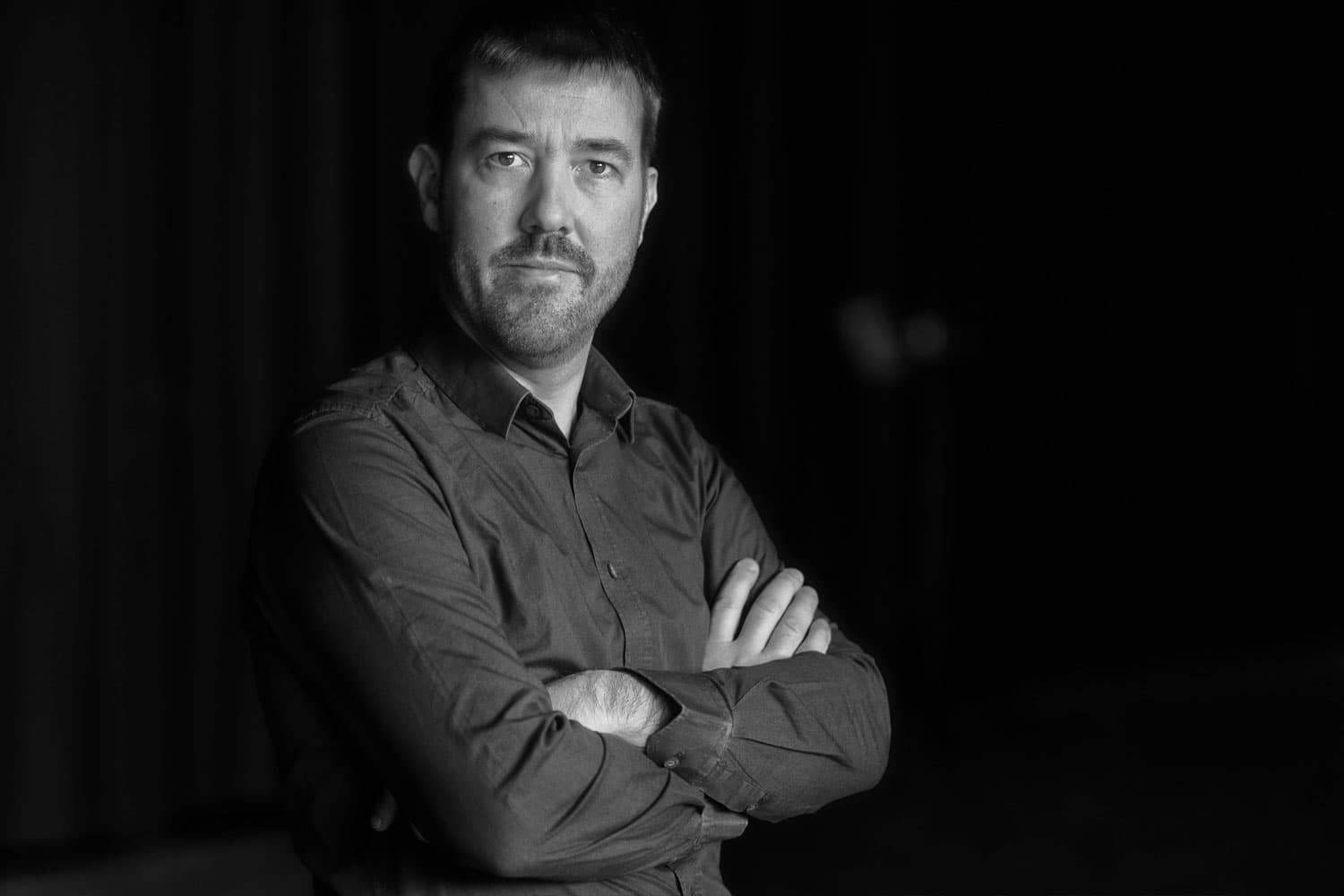
Bart Onsia is business development manager for the energy storage and conversion activities at imec/EnergyVille. Bart holds a degree in chemical engineering and has over 20 years of experience in advanced semiconductor and energy research and its valorization. He started his career with Bayer as a production manager before joining imec in 1999 as a researcher. In 2007, he became business program manager, boosting the local impact of imec’s energy research and next becoming responsible for business development of imec’s battery and thin-film R&D.
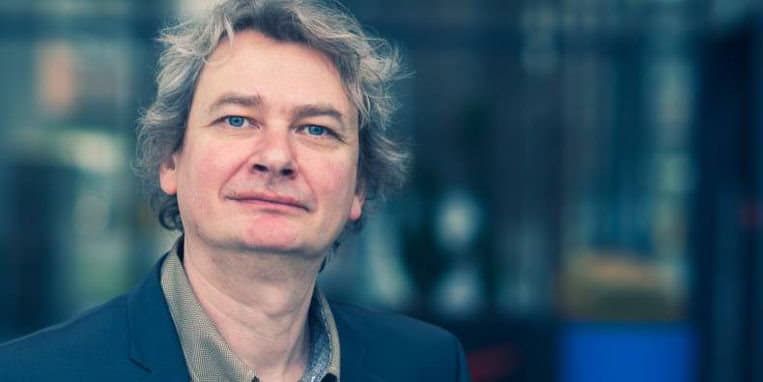
Philippe Vereecken is Scientific Director electrochemical storage and conversion at imec/EnergyVille. He obtained a PhD in physical chemistry in 1998 from Ghent University. After a stay at The Johns Hopkins University as a postdoctoral researcher, he worked at IBM Research (New York) as research staff member (RSM) for several years. Philippe Vereecken joined imec in 2005. After working in the nanomaterials group, he started in 2010 with the energy storage activities at imec. Since 2015, he is part-time Professor at the Department of Microbial and Molecular Systems with the Faculty of Bioscience Engineering at KU Leuven.
Published on:
6 May 2020