Imec and KU Leuven have now bundled their BIPV expertise in the EnergyVille collaboration. They look at how such panels may be engineered into a solution that adds to the building aesthetics, that is easy to install, and that may be produced flexibly and cost-effectively. ‘But foremost, we want to provide total solutions that optimize the energy yield of the building’, say Eszter Voroshazi, Group Leader of the PV module and system team at imec and Dirk Saelens, Professor “Energy in Buildings” at KU Leuven.
Three functions
Dirk Saelens: “Many office and public buildings are clad with large, prefabricated panels, made of glass or opaque materials. These have a double function: they form the outer, protective shell of the building and also determine the aesthetics. We want to add a third function: generating energy. But of course not by mounting standard solar modules, which would be less inefficient, not so good-looking, and would result in all sorts of issues with servicing and electronics. What we are looking for instead are facade panels with integrated solar cells, panels that can be fabricated flexibly and cost-efficiently in a wide range of looks, shapes, and yields.”
Eszter Voroshazi: “Today, the roof-mounted solar panels are assembled from sixty crystalline silicon solar cells in a standard format. They are mass-produced on the other side of the globe and there is no easy and cheap way to make smaller batches in other formats and configurations. Companies will sometimes ask us to cut existing panels to size, but that is impossible because it will destroy the panel. Real BIPV, in contrast, requires a fabrication that assembles the cells together with the other facade elements, in the number, shape, and configuration required by the facade element. This flexible fabrication is also especially suited to add our second type of solar cells: those made from thin-film technology. This is an upcoming technology that even allows making semi-transparent surfaces.”
Flexibly producing facade panels
Dirk Saelens: “To arrive at the ultimate BIPV facade panels, these are the challenges that we have to address: Foremost, it’s about the aesthetics. Panels are designed and chosen to give a building a particular, sometimes unique appeal. If we want BIPV to be taken up by architects, the panels with solar cells will have to be equally appealing. Second is the flexibility in the dimensions of the panels. Even within one building project various panel sizes may be required. This calls for a flexible, automated on-time assembly. And a third challenge has to do with the installation. Traditional facades are normally installed by the facade builder. However, if the panels also contains solar modules, these should be connected to the electrical installation by electricians before the facade is completely closed. In some cases this would require the electricians to come twice, which is obviously not an optimal way of working. In addition, the space behind the panels for the electronics (e.g. the inverters) is very restricted. But even if there were enough space, providing access for servicing or replacement would still be a challenge. The only solution to this conundrum are plug-and-play panels with integrated, miniaturized, high-quality electronics, panels that just have to be hooked up and that don’t require the expertise of an electrician.”
Eszter Voroshazi: “We are working with a local partner, an expert in automation, to automate the assembly of facade panels. Today, the components of custom-sized panels are mainly assembled by hand. This allows for a great flexibility but is also quite inefficient and expensive. To this we now want to add the very delicate solar cells and electronics that have to be integrated with the utmost precision, cleanliness, and reliability. So that calls for a new generation of assembly tools, a first one of which will be installed in our EnergyVille labs soon. Ultimately, we see this evolving to a situation where a computer program automatically generates the panel designs from the architect’s design and the building’s energy requirements. These are then translated to instructions for the panel assembly robots.”
What is possible today?
Dirk Saelens: “At the KU Leuven, we already have a test and demonstrator setup where we can integrate and monitor facade panels in various configurations. But now, on the new EnergyVille campus, there is a dedicated building where we have 15 slots to hook up facade panels. This allows to test and compare panels of various compositions and configuration for extended periods of time, during winter and summer. They are connected to our monitoring equipment that allows us to measure the yield, ventilation, and physical properties of the building, and to mimic an environment that also includes e.g. storage systems or a DC grid.”
“To arrive at a realistic setup for office buildings, the EnergyVille facades are oriented East, South, and West. With panels on three sides of a building, BIPV can provide energy during a large part of the day, starting as early as possible and stretching out over the day. This much more matches the energy consumption patterns in buildings than would be the case with a South-oriented roof-mounted panels that are optimized to generate an energy peak only when the sun is at its highest.”
Eszter Voroshazi: “Where are we today? What can we offer architects, engineering bureaus or facade manufacturers? For one, our experts from imec and KU Leuven can take a building design and translate it into its energy requirements (e.g. energy needs varying through the day, options for sustainable generation, AC/DC grid comparison, cooling and heating simulations…). Then we explore the selection of the technology (type of cells, electronics, connections…). Next, we assemble one or more prototypes with surfaces of up to 10-20 m2. And if these are validated, we can set up the technology transfer to a facade manufacturer to have the necessary volumes and surfaces produced. So today, we’ve already assembled and tested a number of panels and we’re ready for many more.”
Dirk Saelens: “BIPV is an exciting domain on the crossroads of engineering and research. We have the technologies ready that can be used today, and we can help develop practical solutions for companies. Beyond that, there are still many roads to explore, roads to higher efficiencies, arbitrarily complex shapes, plug and play concepts with integrated miniaturized electronics, integrated battery storage, fully automated assembly… With all expertise we now bring together in a single lab, the EnergyVille collaboration is uniquely positioned to do that R&D and to form the forefront of European BIPV. We invite panel manufacturers to join and help us develop a new generation of BIPV products, as they may provide a unique competitive advantage for sustainable building.”
Opening of EnergyVille 2
The new offices and labs of the EnergyVille collaboration are situated at Thor Park, part of the former mining site in Waterschei, Belgium. The initiative brings together researchers from KU Leuven, VITO, imec and UHasselt to work on research into sustainable energy and intelligent energy systems. A second EnergyVille building was opened officially on 31 May 2018. Some 100 researchers will be working at the new facility to develop, amongst others, BIPV panels, but also e.g. new thin-film solar technology and a new type of solid-state battery for applications such as electric vehicles and energy storage.
Want to know more?
- A fresh look at assembling PV modules: a woven fabric interconnects and encapsulates, a blog entry of Eszter Voroshazi in PVTech.
- A forecaster for solar panels, an article in the May 2018 edition of imec magazine.
- Rethinking the home grid – a case for direct current, an article in the June 2017 edition of imec magazine.
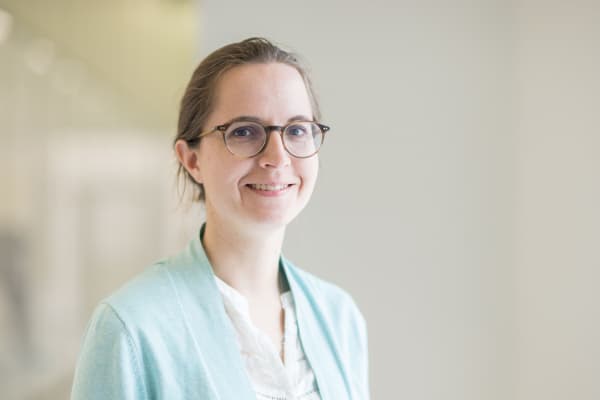
Eszter Voroshazi is the group leader of the module and system activities at imec. She holds and engineering degree from INSA de Rennes (2008, France) and a Ph.D. from the KU Leuven (2008, Belgium). Currently, she works in the frame of the EnergyVille collaboration focusing on the development of innovative PV module technologies and materials, energy yield prediction, and BIPV. Next to this she serves as expert in PV standardization committees, and as reviewer to scientific funding agencies, conferences and journals. She is the co-author of 80+ papers with an h-index of 18.
Dirk Saelens is professor “Energy in Buildings” at the Department of Civil Engineering KU Leuven (Belgium). He is responsible for the academic aspects of Buildings and Districts within EnergyVille. His main area of expertise is the assessment of energy and comfort in buildings and urban environments through measurements and building simulation. Dirk Saelens obtained his MSc in architectural engineering from the KU Leuven in 1997 and his PhD in Civil Engineering in 2002, researching ventilated double-skin facades.
Published on:
30 May 2018