In the coming years, tandem modules combining silicon PV and perovskite solar cells will become available. Using these modules in novel integrated solar solutions will demand for customized dedicated ways of working and requires a close link with local market players and customers. This presents Europe a unique opportunity to regain an important role in solar manufacturing.
Solar energy is quickly becoming the cheapest source of electricity, both in the EU and worldwide. Along with the declining cost of solar modules, PV manufacturing has transformed into a mass-producing industry and made a shift to Asia. Many European PV companies have been pushed out of the market, leading to a dramatic reduction of the PV production capacity in Europe. However, strong technical expertise on equipment manufacturing and excellent research capacity is still present on the old continent. How can Europe, once the world leader in the manufacturing of solar panels, regain a key role in this fast-growing market?
The success of today’s PV industry is based on scaling up manufacturing capacity and on maximal standardization of current PV products to ensure maximal cost reduction. For traditional single junction silicon solar cells, the power conversion efficiency has a theoretical limit just below 30 percent. After years of successful technological innovation, the efficiency of industrial solar cells is leveling off towards this value, resulting in significant extra efforts that will be needed for limited improvement.
However, we can surpass the efficiency limitations of a single junction by capturing solar energy from a wider wavelength range. For this, we should stack two (or even more) different semiconductors on top of each other, each sensitive to a distinct part of the light spectrum. By combining the right set of materials, a larger portion of the available light can be converted into electricity compared to single junctions.
Fig. 1. Schematic of a tandem solar cell comprising two solar cells with descending bandgap energies. Incident photons with energies above the bandgap of the top solar cell are harvested at a higher voltage by the wider-bandgap top solar cell. The lower-energy (longer-wavelength) photons transmitted by the top solar cell are harvested by the bottom solar cell.
Compound semiconductor-based tandem solar cells have been widely used for e.g. space applications, but because of their high material cost the technology didn’t result in large-scale terrestrial applications. To introduce tandem cells in the terrestrial PV market dominated by c-Si (crystalline Silicon) solar cells, adding a low-cost absorber on top of the c-Si cell is the most promising route. Until a few years ago, there was a lack of an efficient material that could be used in a tandem configuration with the PV technologies established in the market. However, the advent of perovskite solar cells and their rapid progress has changed the status quo.
Research groups and companies from different European regions have set up research programs to develop perovskite based solar cells and to make them ready for large-scale production. A key example is Solliance, a partnership of R&D organizations from the Netherlands, Belgium and Germany. Imec, as a partner in Solliance, reported already in 2018 a fully scalable tandem solar module employing a perovskite top solar module stacked onto an interdigitated back contacted c-Si bottom solar cell. Both devices have an identical aperture area of 4 cm². With a combination of optimized transparent electrodes and efficient module design, this multi-junction solar module exhibited a power conversion efficiency of 25.3%.
Fig. 2: Tandems with aperture area of 4cm2 with upscaled processing for the front perovskite modules
The tandem modules that Solliance initially designed and tested were so-called 4-terminal modules (fig. 3, left). In this configuration, designed to always reach maximal performance in varying illumination conditions, the two subcells of the tandem are electrically isolated, each having their own wiring. As a result, the finished product has four electrical wires coming out and therefore requires an additional convertor. In a 2-terminal module (fig. 3, right), in contrast, the two subcells are electrically connected in series. The advantage is that the module has only two terminal wires, but the series connection requires the currents to match. This constraint results in a suboptimal total performance. So, both tandem configurations have advantages and disadvantages, and the boundary conditions of the application may decide which solution is used in which circumstance. Hence, at imec and together with our Solliance partners we work on both tandem configurations.
Fig. 3: Schematic representation of the two main tandem architectures investigated nowadays; (left) four-terminal configuration with electrically isolated perovskite top and Si bottom cell; (right) two-terminal configuration whereby the top and bottom cell are electrically connected in series
Besides the perovskite top-cell, a bottom-cell is needed to assembly the tandem solar cell. Although CIGS cells could be used as bottom-cell as well, because of availability and cost silicon cells are the most obvious choice. Most of the modules that are currently being manufactured within the EU are mainly based on imported c-Si cells with a high carbon footprint. However, there are some initiatives pending to set up a silicon heterojunction cell factory in Europe. Meyer Burger, a large equipment supplier, recently announced that it is evaluating the feasibility of becoming a volume producer of heterojunction solar cells and modules in Europe. Last year, Burger also invested in Oxford PV, a start-up that plans to produce perovskite tandem solar cells.
At the same time, a unique consortium of European research institutes and industry partners joined forces to develop knowledge-based manufacturing technology, at both the cell and module level. This HighLite project coordinated by imec, received €12.9 million funding from the European Commission to increase the competitiveness of the EU PV manufacturing industry. To reduce the cost and carbon footprint, the project focuses on ultra-thin (down to 100 μm corresponding to about half of the current thickness) c-Si cells. To improve performance and durability, the cells are being designed with advanced re-passivation techniques in such a way that they can be cut into halves or quarters. By cutting the cells in halves, the current generated from each cut-cell is halved, which reduces resistive losses. Industrial tools will be developed to assemble these cut-cells into high-efficiency modules. The 3-year project will demonstrate these new production solutions on pilot-line-level by preparing two competing technologies for possible manufacturing in Europe.
The first silicon cell technology explored in the Highlite project is based on back-contact assembly of interdigitated back-contact (IBC) cut-cells. In IBC-cells all the contacts are put on the back side. The big advantage is an increased performance, because there is no optical shading from contacts at the front side of the cell. Tandems using IBC cells can be made in a 4-terminal configuration with a simplified interface between silicon and perovskite (or in a 3-terminal configuration which is a combination of both techniques).
The second technology is based on shingled assembly of 2-side contacted silicon heterojunction (SHJ) cut-cells. These 2-side contacted cells can be easily used in tandem cells with a 2-terminal configuration because of the use of a transparent conductive oxide (TCO) on both the SHJ and perovskite cells. In a shingled version the SHJ cut-cells will be assembled with overlapping edges (like roof tiles), leading to a uniform look. This is not only aesthetically pleasing, but also more efficient as there will be limited shading from the connections. In the project, both SHJ and IBC technologies will be tailored for various applications including building-applied PV (BAPV), building-integrated PV (BIPV) and vehicle-integrated PV (VIPV).
At imec we’ve set out a roadmap to bring the tandem cells and modules to technology levels ready for product integration (depicted in Fig.4). Applications where a maximum power on a limited area is desired are expected to be first markets, such as VIPV. Following capacity growth through the early application fields, BIPV and the utility scale will become accessible.
Fig. 4: Imec’s technology roadmap to realize product-ready tandem technology in the coming years, for different application areas, ranging from vehicle over building integrated PV to utility scale deployment.
With the integrated PV market supported by BIPV and VIPV, a next wave of solar growth opens up an opportunity for European industry to develop new superior manufacturing facilities. Of course, there is still a risk that the production of tandem modules will move to Asia once they become a standardized product, similarly to what happened to single junction silicon production. However, the challenge now is fundamentally different because there will be a strong demand for customized dedicated solutions.
European legislation requires new buildings to be nearly zero-energy by the end of 2020. Solar energy is the most cost-effective way to power these buildings. On high rise buildings, with limited roof surface, high-efficient tandem solar cells can be used in facade elements to enhance energy yield, while pure, semi-transparent perovskite modules can be used as a substitute for glass walls. Because each architecture is different, this will require customized solutions. When an architect observes for instance a deviation from the building plans, adjustments to the modules might be needed.
At present, a lot of manual interventions are involved in these custom-module designs. With increasing volumes, there will be a strong need for assembly technologies that allow mass customization of modules. In the last few years imec has developed an innovative module technology using solder coated conductive interconnection wires woven into the module encapsulant material. In this way the cell interconnection and module lamination can be done in one step. Moreover, the technology allows straightforward and automated customization of module size and cell spacing.
The implementation of such customized modules for different applications opens up a market with new challenges. PV manufactures will need to interact more closely and directly with local players and customers in order to respond to their needs. For Europe, this forms an opportunity to create more secure and sustainable supply chains and to regain a part of the fast-growing PV market. For new players, this forms a real opportunity to join this European PV market.
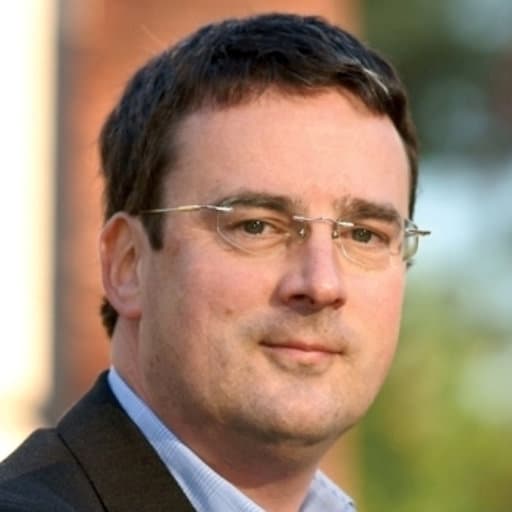
Philip Pieters is business development director energy at imec/EnergyVille/Solliance. He obtained a PhD. in electrical engineering from KU Leuven (Belgium). Dr. Pieters joined imec in 1994 as a researcher and moved into business development in 2002. He’s responsible for imec’s energy business development encompassing solar, energy storage and energy conversion technologies.
Imec is partner in EnergyVille, a research collaboration in Belgium between KU Leuven, vito, imec and UHasselt in the field of sustainable and intelligent energy systems.
Imec and TNO are also leading partners in Solliance, a research collaboration between R&D institutes and universities from The Netherlands, Belgium and Germany on thin film photovoltaic solar energy.
Published on:
3 June 2020