Microchips have enabled tremendous progress in many industries, including the medical arena. Just think of hospital instrumentation, wearables and implantables becoming ever smaller, faster, more energy-efficient and versatile.
ASICs as the next step in MedTech innovation
Whereas most medical devices use standard (off-the-shelf) microchips for communication, sensing, powering etc., more and more companies are considering the use of application-specific chips or ASICs. These chips have many advantages:
- an ASIC, designed for a specific application of the customer, is always smaller than a solution with multiple standard chips
- ASICs use less electrical power and perform better for the specific application
- they are the best choice in terms of IP protection
- assembly/packaging of an ASIC is less costly and can be customized for the application – even if it requires an initial investment for ASIC development
Imec has set up a division – imec.IC-link – that focuses solely on ASIC development for external customers, covering all the different aspects of the workflow.
Another indispensable asset of imec.IC-link is the extensive network that imec has set up with all players in semiconductor manufacturing. From this, imec.IC-link derives strategic alliances with chip manufacturers, more specifically foundries, to develop the ASICs at the right time and at the right price, with access to all possible technologies on the market – older ones as well as the most advanced.
Imec.IC-link uses strategies to reduce the cost of first prototype ASICs to do the validation. For example, multi-project wafers (MPW) combine chips of different customers onto one substrate and multi-layer masks (MLM) house several design layers on one mask.
Process optimization, covering all layers of ASIC development
The development of an ASIC requires many successive steps. However, they are intertwined and decisions in the final steps influence earlier ones. Therefore, it is important that an interdisciplinary team works on the project and that there is a single point of contact for all the different parts in the chain.
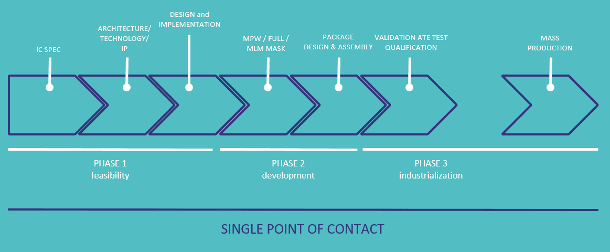
A typical ASIC development flow
An important step of the ASIC workflow, that often influences earlier ones, is the choice for a specific packaging solution. Innovations in packaging are very important for medical products (small size, specific form factor, biocompatibility). Also in this field, imec.IC-link benefits from imec’s extensive knowledge and R&D on new packaging concepts.

Innovative packaging concepts are an indispensable part of the ASIC development workflow.
Why CAIRDAC uses ASICs for their ‘powered-by-heartbeats’ pacemaker
The French start-up CAIRDAC is developing an extremely small pacemaker that can be implanted endoscopically, thereby significantly reducing risks of infections and other complications, and that uses the kinetic energy of the heart to power the device. They are currently in the preclinical testing stage of their product with the first in-human testing being planned for early 2023.
The device uses three ASICs: the power management unit, the CPU and the therapy pacemaker function. For two of these, they worked with imec.IC-link:
- the power management ASIC was designed together with Shortlink, a Swedish design house, and the tape-out was done through the imec EUROPRACTICE service
- the therapy ASIC was developed by IC’Alps, a French ASIC design house and strategic member of the Design & IP Partner Network of imec.IC-link. The plan is to integrate all functionality into a single ASIC
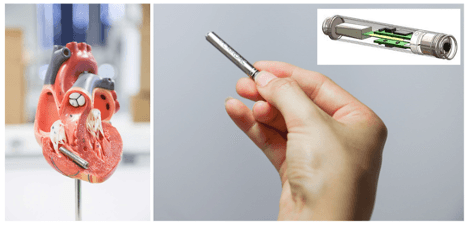
The innovative pacemaker solution of CAIRDAC, relying on three separate ASICs which in the future will be combined into one.
Why Capri Medical needs ASICs to combat chronic migraine
The small Irish start-up company Capri Medical aims to cure chronic migraine with a nerve-stimulation implant, powered by a control device and complemented by a smartphone app. Because of the small size of the implant, it can be administered with an injection and a 20-minute procedure (instead of the traditional 3-hour surgery).
The company worked with imec.IC-link to develop a dedicated chip solution, because of the miniaturization aspect (an injectable chip!), the integration of multiple functionalities, and the cost aspect.
Multiple design iterations were done in TSMC 180nm technology and resulted in a 1.4 x 1.4 mm die. It was taped out on a multi-project wafer. The 180nm technology was chosen as a starting point since it’s the most cost-effective for the first prototype. Once the design is validated, the team will investigate if it can be made even smaller by moving to smaller technology nodes (such as 55nm).
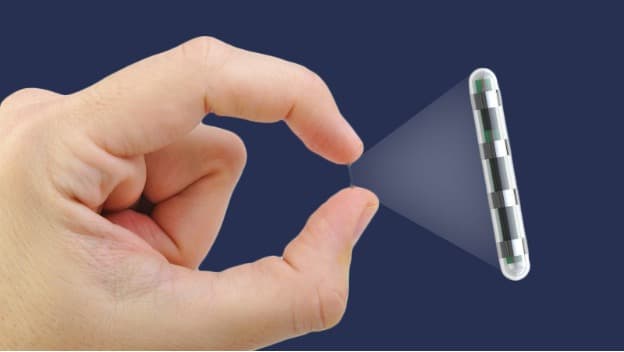
The injectable nerve-stimulation device to beat chronic migraine, by Capri Medical
Want to know more?
- Imec.IC-link is part of the global R&D hub imec, and provides access to advanced ASIC foundry technologies. Its services are available to customers worldwide and teams are based in Europe, the USA, China, India, Japan, Brazil and Israel. More info: www.imeciclink.com
- Read the full story of CAIRDAC and Capri Medical on the dedicated imec.IC-link website
Published on:
18 November 2021