The first automobile, a marvel of technological innovation, hit the road nearly 150 years ago. Undoubtedly a great achievement – yet one that pales in comparison to the challenges car manufacturers face today.
One particularly pressing matter is the development of high-performance EV platforms now that the age of fossil fuel-powered cars is ending. In parallel, new road safety initiatives call for smart driver assistance systems to make on-the-fly collision avoidance decisions. And all the while, semiconductor shortages, and geopolitical upheaval require the industry to rethink its long-standing partnerships and supply chain arrangements. In other words, a perfect storm is brewing – and major disruption is coming.
While pressure is mounting, many car builders remain in doubt about how to address these challenges properly. One critical success factor will be for them to reclaim the steering wheel and start driving their own roadmaps and architectures again – instead of relying too much on suppliers’ strategic choices. This will require the entire ecosystem to reinvent its R&D practices and collaboration models.
An ecosystem in turmoil
The automotive industry has a rich tradition of successful collaboration. As soon as car manufacturing entered the era of mass production, car builders joined forces with selected (tier 1) suppliers to develop tailor-made parts – ranging from engines and brakes to car seats. Later, an ecosystem of subcontractors rallied around them to produce the underlying (silicon) components. It allowed the automotive supply chain to pursue thorough specialization and cost optimization for many years.
Today, however, this landscape has drastically changed. Cars have transformed from purely mechanical devices into software-defined electric vehicles (EVs) that rely on dozens of sensors, complex algorithms, and high-performance computing to do their magic. It has made the process of building a car more intricate than ever. Hence, it should not come as a surprise that specialist electronics and semiconductor companies have moved up the automotive value chain, displacing many of the traditional tier 1 suppliers.
And further disruption is on the horizon, fueled by a stagnant market and the escalating R&D expenses that come with the development of vehicles featuring even more advanced safety and in-vehicle entertainment options. It leaves only a few suppliers able to produce cars’ smart systems. In response, car manufacturers are embracing a new approach, collaborating even more intensively with semiconductor foundries and providers of semiconductor solutions to avoid vendor lock-in and mitigate potential supply chain disruptions.
In other words, it is safe to say the automotive ecosystem is in turmoil, with questions being raised about the potential collapse of the industry's once-so-great collaboration models. Is this a reason to panic? Perhaps not. The solution could arise from a surprising source and be much smaller in scale than one could envision.
A tiny solution to a grand challenge
Dr. Gordon Moore, the late co-founder of Intel, once suggested that it might be more cost-effective to construct large systems by assembling smaller, individually packaged, and interconnected components – rather than cramming all the necessary elements onto a single, monolithic chip.
This principle forms the foundation of a chip design that is bound to change how car manufacturers build their vehicles. It is an approach that relies on seamlessly combining ‘chiplets,’ miniature modular chips meticulously designed to efficiently perform specific functions, to form more sophisticated integrated circuits (akin to Lego building blocks). For instance, it would allow car builders that require substantial processing power for an AI-based pedestrian detection application to substitute today’s conventional CPU with a chiplet explicitly designed for that purpose.
Chiplets offer numerous advantages over traditional monolithic chip designs. Firstly, they can be easily and swiftly customized and upgraded, which translates into reduced development time and costs. This agility enables manufacturers to promptly adapt to evolving market demands and emerging technological advancements. And it allows car manufacturers (and their tier 1 suppliers) to mix and match subcontractors’ components more flexibly, eliminating the risk of vendor lock-in and fostering a more robust, healthy, and dynamic supply chain.
Secondly, as chiplets are optimized for specific tasks, they come with enhanced performance. In turn, this facilitates the reduction of processor size and power requirements. After all, by consolidating multiple functions into compact units, chiplets eliminate the need for extensive wiring, cooling systems, and other components inherent in conventional chips. Consequently, manufacturing costs decrease, and smaller device designs become feasible.
No interoperability, compatibility, or scalability without renewed collaboration agreements
While chiplet technology is relatively new, several semiconductor companies are already actively developing it. Still, to ensure its widespread adoption in the automotive sector, a dedicated effort is required; one that involves the creation of automotive chiplet reference architectures – and standards – to ensure the technology’s interoperability, compatibility, and scalability, translating into a reduced time-to-market.
This will require the automotive supply chain to find a new equilibrium and investigate renewed collaboration models. After all, it is only by combining their strengths that semiconductor manufacturers, automotive companies, and technology providers will be able to accelerate innovation, and ensure seamless integration of chiplets into tomorrow’s cars.
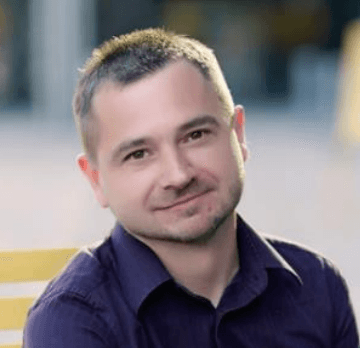
Bart Placklé holds a Master of Science degree and a postgraduate degree in telecommunications from the University of Hasselt (Belgium), and imec (Leuven, Belgium), respectively. He also obtained a postgraduate degree in executive business economics from KU Leuven (Belgium).
Bart started his career at Acunia, an imec spinoff, where he initially served as a lead silicon designer and later advanced to become the general manager of the hardware business unit.
In 2004, Bart joined Intel to create the company’s in-vehicle infotainment business. As chief architect and later automotive CTO, he led the development of five generations of high-performance automotive solutions, driving Intel’s automotive segment to become a multibillion-dollar business. In recognition of this contribution, Bart received the Intel Achievement Award in 2016. In 2021, Bart was appointed as the CTO of AXG Mobility-as-a-Service at Intel.
In 2023, Bart Placklé returned to imec, assuming the role of vice president of automotive technologies. In this capacity, he is leading the development of cutting-edge solutions that will shape the future of mobility.
Published on:
2 October 2023