Intro
In the domain of flexible electronics, the next five years may very well be the most exciting that we ever witnessed. That is, if we manage to profit from the bounty of opportunities and can overcome the remaining challenges.
Kris Myny, a principal member of imec’s technical staff in the domain of flexible electronics, gives his view on the main challenges and possible applications of flexible electronics.
“Flexible electronics are made by adding layers of suitable materials onto flexible substrates. In contrast to silicon chip processing, fewer steps are needed and the temperatures are much lower."
"The main promise is that flexible electronics will be many times cheaper than today’s electronics."
"Also, we’ll be able to integrate applications directly in any material and with any form factor. If we succeed, that’s enough to herald a new revolution, one in which we can make every object smart.
The main challenge I see is that we now have to look how to scale our infant technology, giving it more juice and making it more energy-efficient at the same time. We know that it can be done in principle, but it will require some patient searching and tuning.
This is what I and other researchers hope to accomplish:
Make transistors smaller and circuits denser.
Today, and certainly in comparison with silicon chip technology, we’ve only demonstrated a few circuits containing a few thousand transistors maximum. We’re still at the beginning of Moore’s Law for flexible electronics, and we should be able to go to 10,000 or even 100,000 transistors per square centimeter at a cost of one dollar cent. That is a density where things start to get interesting, where we could build powerful, innovative applications.
Get a better grip on power consumption.
The best material we currently have is an n-type thin-film semiconductor, a material with access to electrons causing electrical currents to flow between source and drain. Unlike in silicon CMOS technology, we don’t yet have a comparable p-type material that can counterbalance and stop that flow in digital circuits. In our flexible circuits, there are always currents flowing between supply and ground. In the near and mid-term my research is focused on finding circuit solutions, solutions with only n-type transistors that nevertheless reduce these parasitic leakage currents. For complex circuits, it should be possible to lower power consumption with a factor 10 to 100.
Develop new fabrication techniques and tools.
Today, large-scale production of flexible electronics is the realm of the display makers. Their equipment produces features in the micrometer range. If we want to make transistors smaller and circuits denser, we’ll need submicrometer features. So we’ll need to develop a new generation of tools and production lines. So tool makers and manufacturing will need to step up.
Now on the applications! Here are three that I’d like to help develop:
High-density displays for use in bendable, rollable surfaces, glasses, or who knows even in contact lenses. To get a high-quality AR/VR experience, these require small, closely-spaced pixels, an order of magnitude denser than we can produce today.
Wearables or patches that are tacked to the skin and that measure body parameters, e.g. to continuously monitor wound healing without bothering the patient. Longer-term, these could even replace smart watches.
Tags with on-board storage, sensor, and data processing. Imagine we could design tags to check food quality, tags that are tacked onto e.g. apples, cheese packaging, or milk boxes. There you’d need a sensor, with multiparameter sensing including maybe some chemical processing. And you’ll also need processing circuits and a battery to do data analysis when the tag is not within reach of an antenna. The start of the item-level Internet-of-Things?"
"All this is already possible with silicon chips and it may seem a distant dream to reach the same sophistication with flexible electronics. However, if we can boost the density to where I hope we will, and if we can start a Moore’s Law for flexible electronics, then these will definitely become reality."
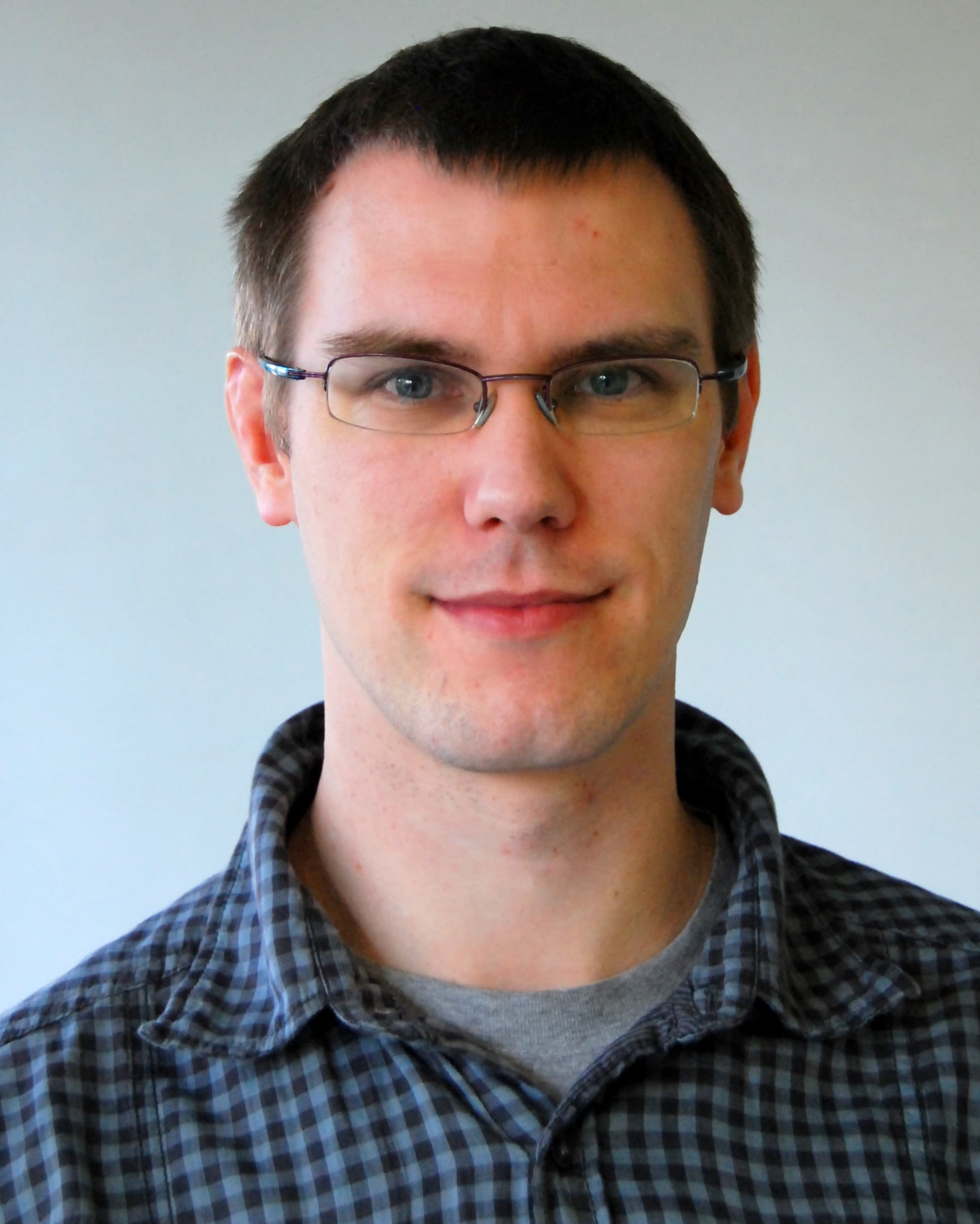
Kris Myny received his MSc in Electrical Engineering from the Katholieke Hogeschool Limburg in 2002. In 2004 he joined imec’s research team and started working on the development of robust plastic circuitry. In 2013 he obtained a PhD at KU Leuven. He is now a Principal Member of Technical Staff at imec and specializes in circuit design for flexible thin-film transistor circuits. His work has been published and presented in numerous international journals and conferences and has received considerable press attention. He was listed as one of Belgium’s top tech pioneers by the business newspaper De Tijd. Last year he also received a prestigious ERC Starting Grant from the European Commission to enable his breakthrough research in thin-film transistor circuits.
Published on:
25 August 2017