This article appeared earlier in Electronics 360 and featured as a podcast in Electronic Engineering Journal.
Improving the efficiency of biological and chemical processes requires precise quality and process control. Gathering the right data and knowledge is crucial in this endeavor to translate process insights into effective interventions. Research towards innovative sensors, accurate simulation models, and well-trained operators is therefore imperative, providing valuable tools in the pursuit of advanced biomanufacturing.
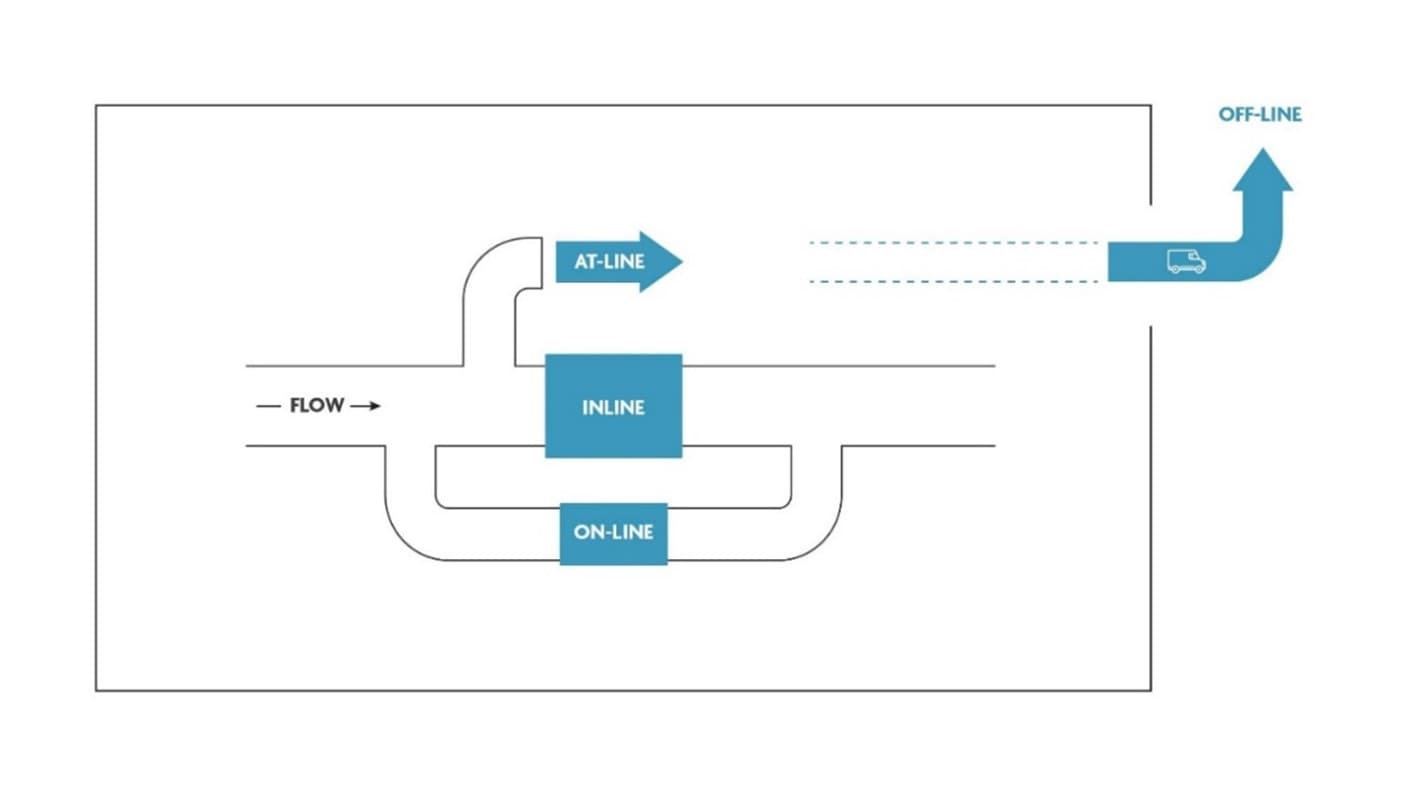
Overview of possible process monitoring
Challenges in precision therapy
Consider the challenges in biomanufacturing, such as the biological production of human cells for CAR-T or stem cell therapy. The process of engineering cells for therapy is lengthy but time-critical for patients. It must be done on a per-patient basis and involves a significant amount of manual labor, making it costly. Additionally, the efficacy of the treatment is directly related to the quality of the final product. These challenges impact clinical relevance, including off-target or nonspecific effects.
Traditionally, biological process control involves 'offline' monitoring, where samples are taken from the flow for later analysis. Such measurements provide a valuable indication of a product's quality at the time of sampling and offer crucial insights for future productions. However, because of the time lag between sampling and analysis, they do not allow for real-time adjustments to the ongoing process. Bringing innovative cell therapies to market affordably, therefore, still requires significant improvement in their process control.
Inline production process monitoring could provide a step towards this necessary improvement. With inline sensors, process steps can be monitored and adjusted in real-time—possibly even automatically. This would not only shorten the total production time and reduce costs but also decrease the consumption of raw materials and energy while improving the quality of the final product.
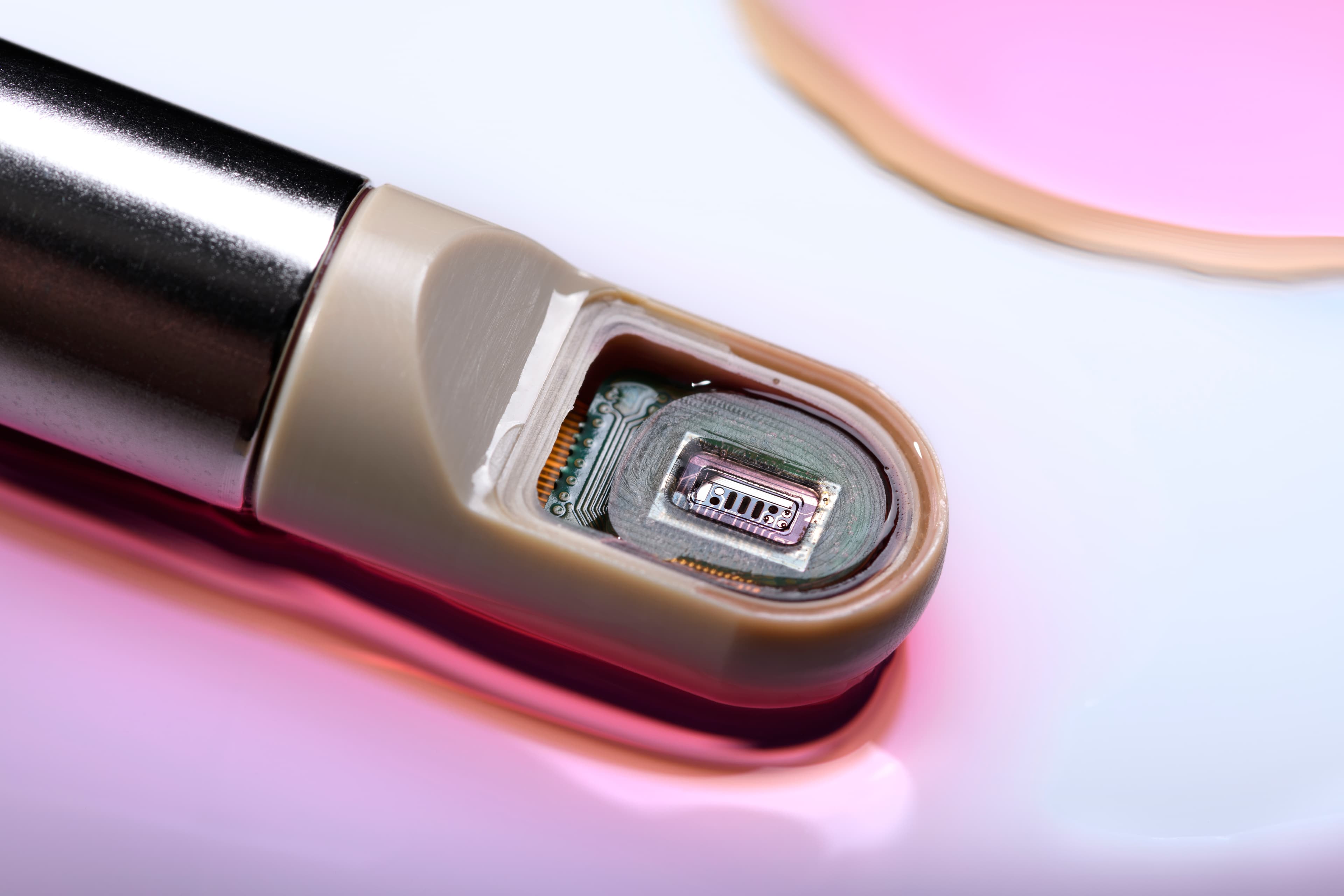
Close-up of a second-generation PAT sensor
Miniaturized inline sensor with imec’s chip innovation
While inline sensors exist, they are far from being a commodity. Probes for inline monitoring for example, such as those for pH and temperature in a bioreactor, have existed for over 40 years. However, to measure all relevant parameters for biological production, you need a multitude of probes and offline systems. This causes installation, calibration, data processing, and even sterilization challenges.
Thanks to imec's expertise in chip technology, researchers have successfully miniaturized and combined various inline sensors into one single probe. The resulting integrated, miniaturized, and multi-parametric Process Analytical Technology (PAT) sensor can simultaneously measure temperature, dissolved oxygen, electrical conductivity, glucose, lactate, and even cell density in real-time in, for example, a bioreactor. As a result, biological or chemical processes can be monitored more closely, and product yields and quality increased.
Decoding process complexity with AI
Inline sensors enable the collection of substantial measurement data, which is essential for understanding the complexity and unpredictability of (bio)chemical processes. However, analyzing and interpreting this sensor data necessitates advanced models that blend real-time measurements with historical data and specific patterns.
By leveraging artificial intelligence (AI), accurate and detailed predictions of critical quality attributes (CQAs) can be generated, which are often challenging to measure directly. This enhanced insight provides crucial information for manufacturing sites to intervene promptly, ensuring quality and avoiding unnecessary costs and time losses.
As an example, together with Leuven University and industry partners, imec optimized a Johnson & Johnson pharmaceutical recipe, reducing solvent usage, time, and costs by up to 30 percent, with less waste production, a purer product, and energy savings of up to 10 percent. By developing a hybrid simulation and optimization platform based on deep reinforcement learning, which combined process measurements with specific domain knowledge (such as chemical reaction progress), thousands of virtual experiments could be executed – an unattainable scale at the fab level.
The project showcased the added value of introducing AI in a fab setting, even on a small scale and with sparse and limited data. This is often the reality when working with sensitive products in bioreactors. As more advanced sensors are integrated into the process flow, the scalability of AI-driven technology will further improve.
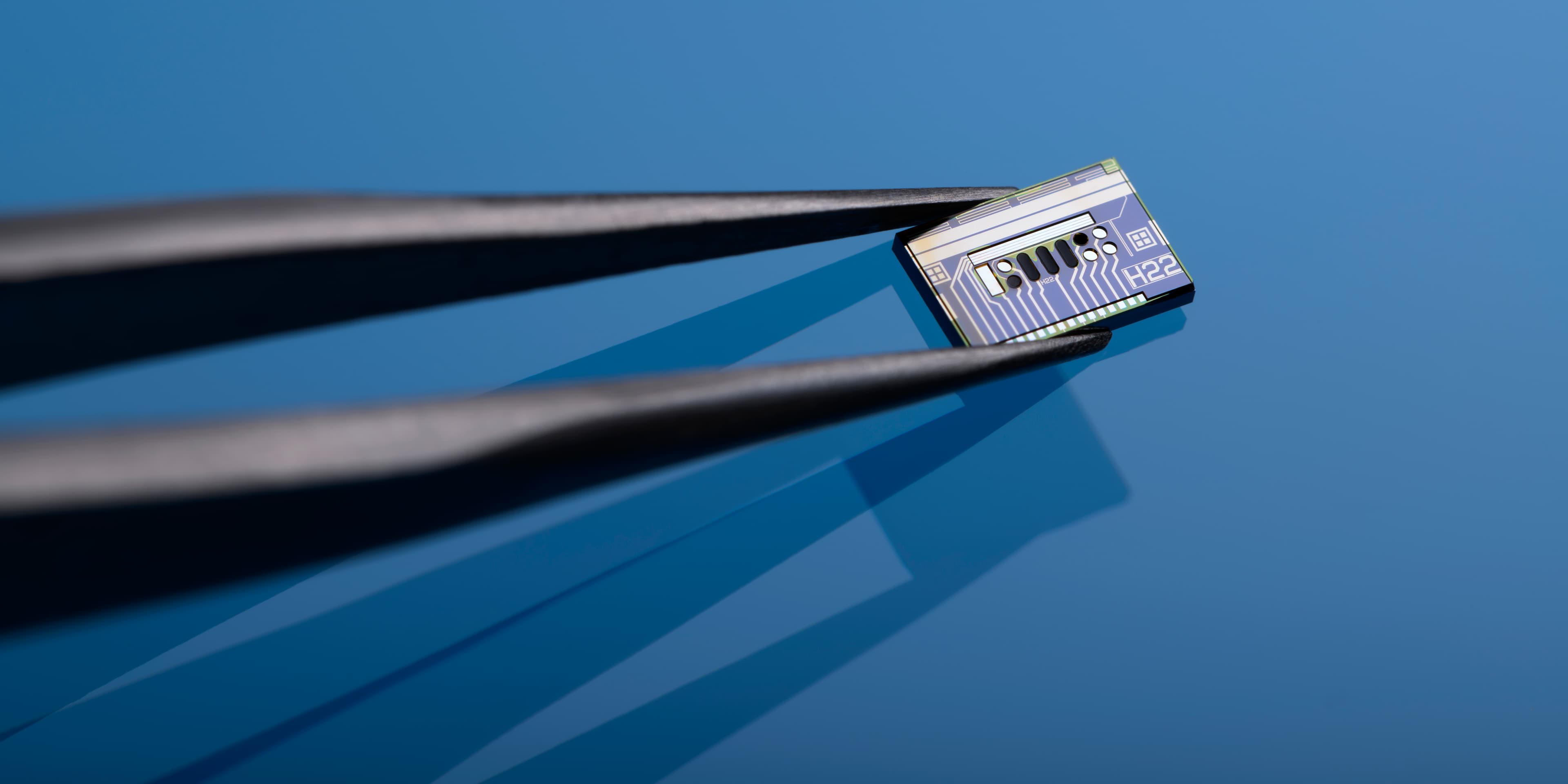
Photo of a second-generation PAT sensor chip. The image shows the sensor chip and the printed circuit board (PCB) on which the chip is mounted. In a fully assembled probe, a cover protects the PCB connections, exposing only the sensor chip to the surrounding fluid
From mysterious model to educator and collaborator
Despite the undeniable benefits of AI, its implementation in the industry remains limited, partly due to its 'black box' nature. As a solution, transparent and 'explainable' AI, which provides an interface explaining decision-making processes in understandable human language, can build trust among human operators and enhance interaction with the technology.
Moreover, transparent AI can potentially educate operators, not just inform them. Years of experience are typically needed to understand and control critical process steps. With AI assistance, the learning curve for less experienced operators can be significantly shortened, increasing their independence and effectiveness. Conversely, AI models can also learn from the expertise of operators.
In another project with industry partners, imec demonstrated the implementation of such a model and its value: first, by digitizing the production process, then linking it to an AI model for its optimization, and finally allowing interaction with operators. Experts were able to identify correlations between measurements and production processes, such as temperature or viscosity. Sensor information could thus be contextualized through human knowledge, considering factors like seniority and historical accuracy. This allowed the AI model to learn based on the expert's input and underlying experience. In this project, such a structured approach resulted in new process insights and optimization of the production of resins (allnex Belgium), improved stability, and faster time-to-market fabric softeners (Procter & Gamble).
Harnessing hardware, human expertise, and AI for innovation
Data and knowledge constraints have traditionally limited steering (bio)chemical processes. Sensors like Process Analytical Technology (PAT) optimize data collection, while AI-driven solutions, supported by existing human expertise, drive innovation in knowledge. As imec's research projects have shown, the synergy between this advanced hardware, expert knowledge, and AI results in more efficient processes, reduced waste, and unprecedented opportunities for innovation.
By bringing this expertise together, research centers can underscore a paradigm shift in the (bio)chemical industry, inviting industry partners to actively collaborate to stay at the forefront of process optimization developments.
Interested in bringing these groundbreaking innovations to the biomanufacturing market and increasing the value of your portfolio? Contact Miranda Noblesse (Miranda.Noblesse@imec.be).
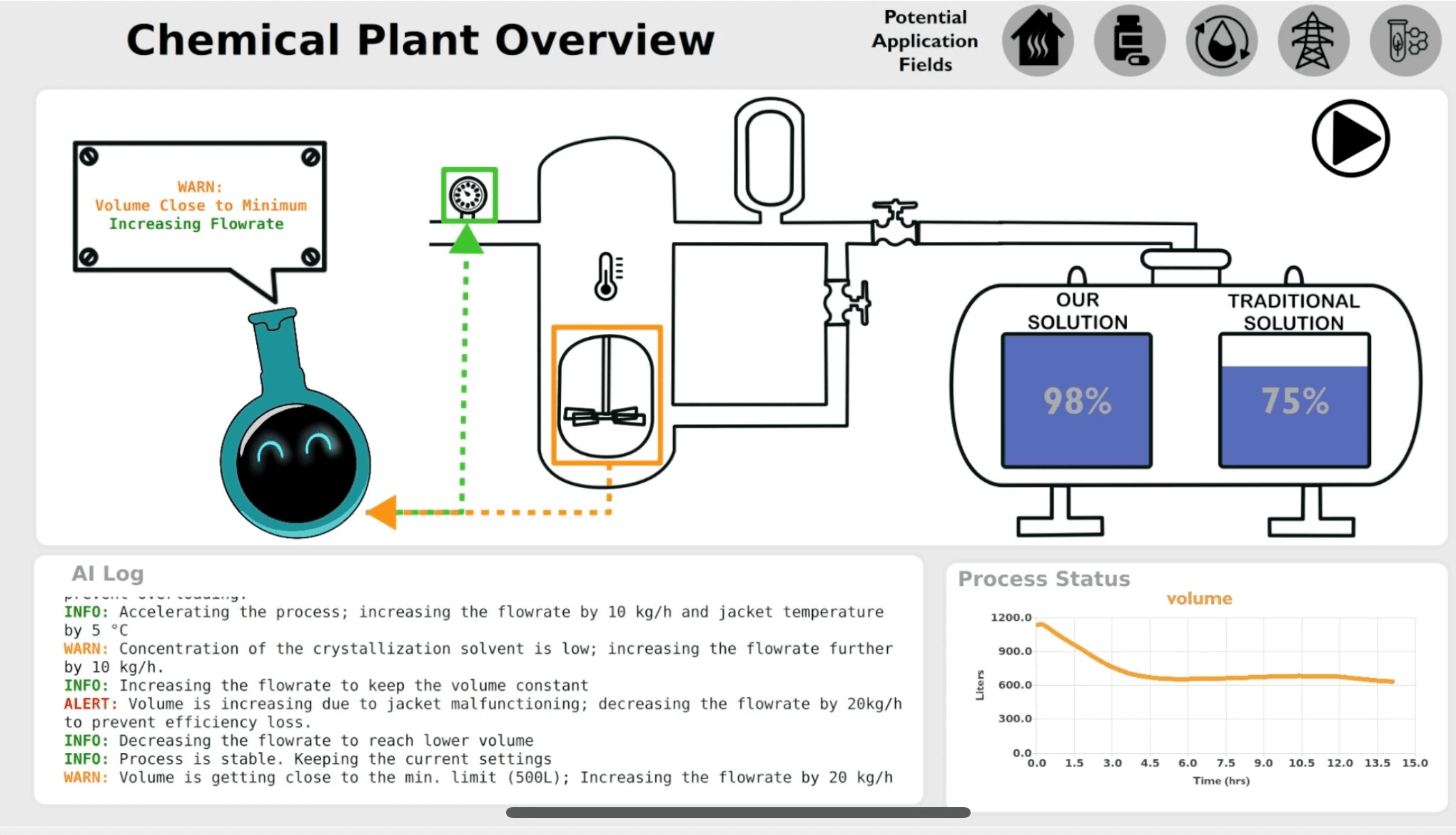
Illustration of an explainable AI demo dashboard (DAP2CHEM project)
CHAI is an imec.icon research project funded by imec and the Agency for Innovation and Entrepreneurship (VLAIO), running until March 2024. The CHAI consortium includes industry partners allnex Belgium, Dotdash, Procter & Gamble Services Company, and research centers IDLab Data Science Lab (UGent), IDLab IBCN (UGent), and IDLab MOSAIC (UAntwerpen).
DAP2CHEM is an innovation project under the umbrella of Catalisti, the spearhead cluster accelerating innovation in the chemical and plastics industry in Flanders. The project ran until September 2022 and was supported by Flanders Innovation & Entrepreneurship (VLAIO). The DAP2CHEM consortium included partners imec (IDLab University of Antwerp), Leuven University, Flanders Make, Ajinomoto OmniChem, Cronos Group, Johnson & Johnson (Janssen Belgium), and Procter & Gamble Services Company.
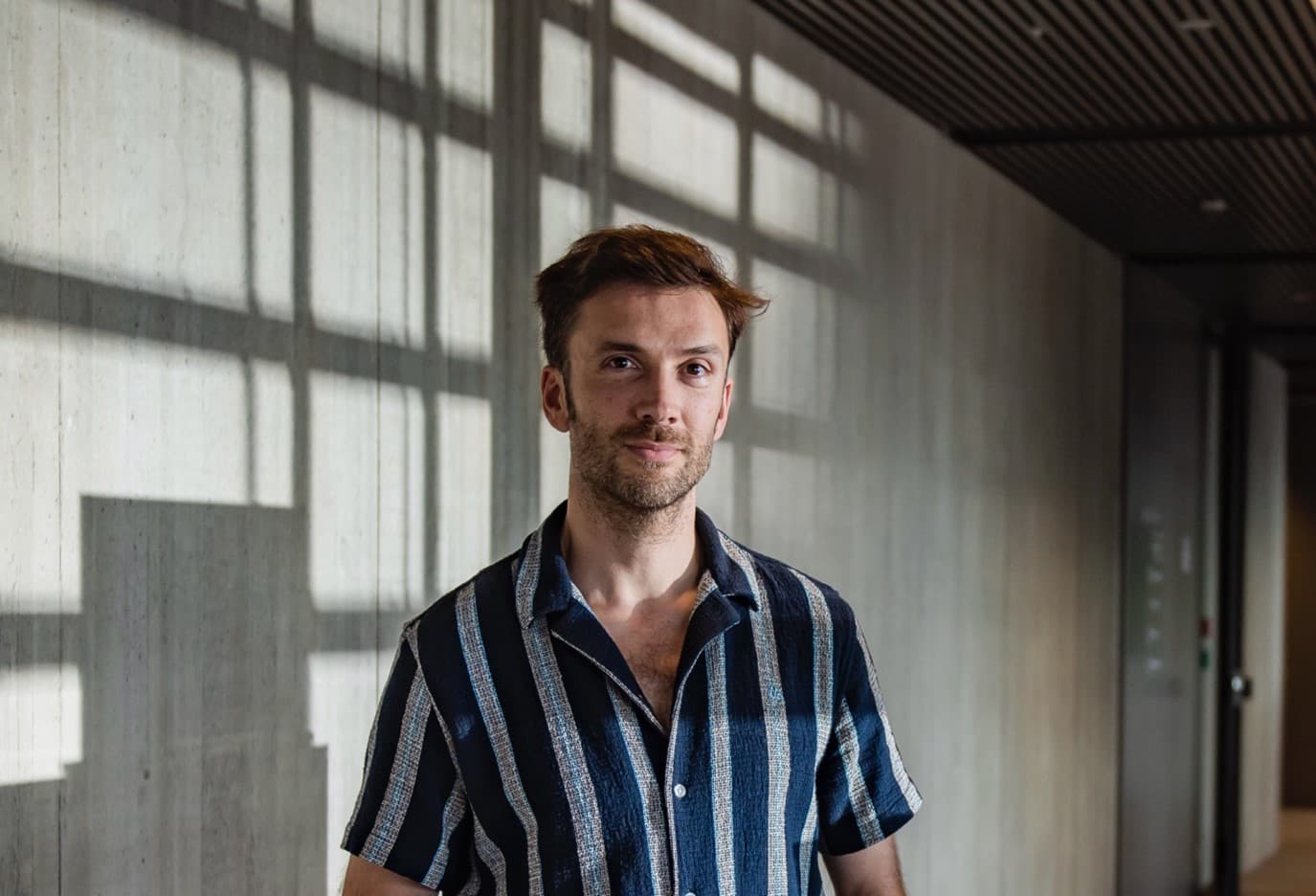
Dr. Michaël Rademaker earned his Ph.D. in Applied Biological Sciences (Chemistry/Applied Mathematics) from Ghent University in 2009. Since 2020, he has been a Business Developer at imec-IDLab, guiding projects from initial ideas to execution. His focus is on AI applications in healthcare. If time permits, he still enjoys writing code weekly. (Photo credits: Karel Duerinckx)
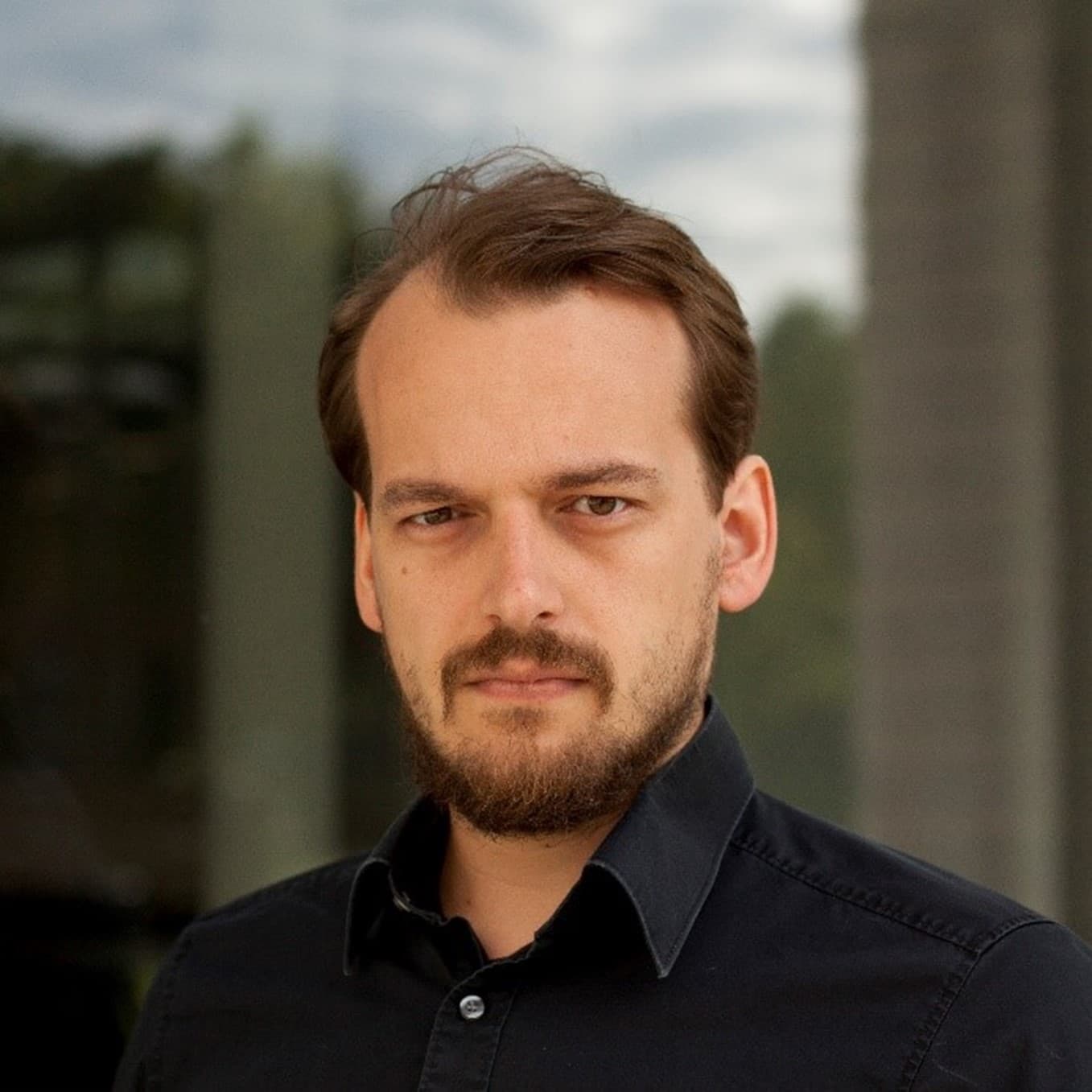
Prof. Siegfried Mercelis obtained his Ph.D. in Applied Engineering Sciences from the University of Antwerp in 2016, where he has been active at imec-IDLab since then. He leads the Adaptive Intelligence (ADAPT-I) program, a team of 30 AI researchers dedicated to bridging the gap between fundamental AI research and industry across domains, including (bio)chemical process control, autonomous systems, energy management, and logistics. (Photo credits: Bart Braem)
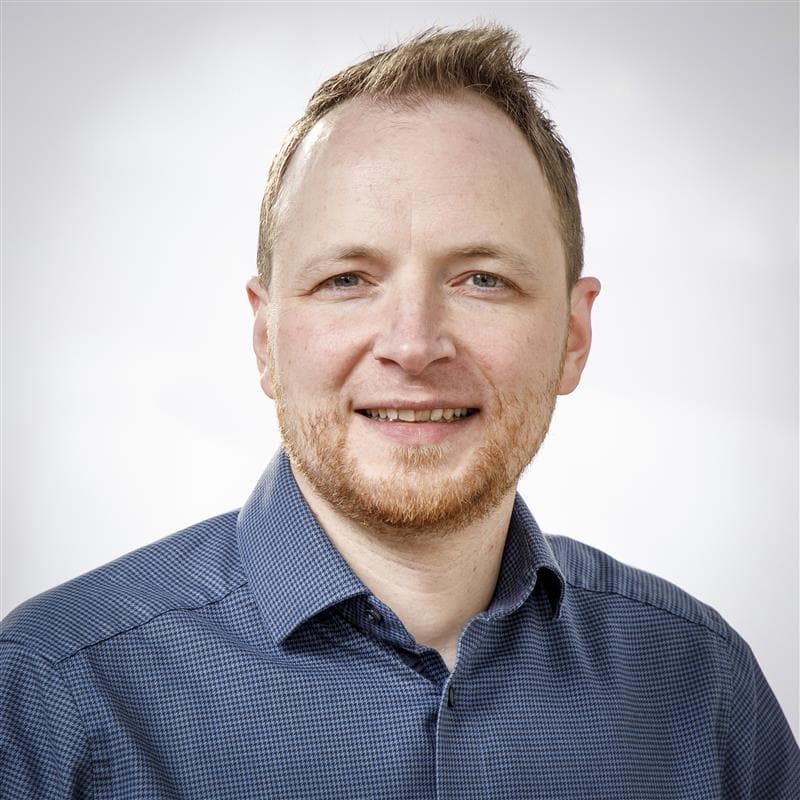
Dr. Bert Verbruggen began his scientific career with a master's in bionanotechnology (Bio-Engineer) at KU Leuven. After a Ph.D. in biosensors and microfluidics, he led various medical product developments, from early research to product launch. At imec, he has overseen multiple projects on process analytical technology and diagnostics since 2020.
Published on:
3 April 2025