Fabric8Labs developed a patented new technique based on electrochemical deposition that will make metal additive manufacturing industry-ready. It is lower cost than laser-based processes, good quality and easy to scale. The technique does not use thermal processes, lasers or powders, but an electrochemical bath and micro-electrode array as a printhead. With the support from imec and imec.xpand the printhead was adapted to use thin film display technology, allowing for high-resolution 3D-structures to be printed.
3D-printing is not only making ideas reality for hobbyists, in the last years it has turned into a full-fledged industrial production technology. As the cornerstone of additive manufacturing – a technology that creates objects by adding layer after layer – metal 3D-printing is rapidly gaining interest over traditional methods for the production of metal parts in engineering, manufacturing, and supply chains. It is fast: a product can be designed, fabricated and tested the same day. It is versatile, allowing parts with complex geometries that don’t need assembly, drilling or even tools. It is precise: small components – moving pieces included – can be printed as a whole in a highly-controlled fashion with extremely precise tolerances and thus improved quality. On top of it all, additive manufacturing generates significantly less waste than traditional methods, up to 90%!
Sounds fantastic, right? Yet, applications so far have been limited to prototyping and most companies are hesitant to adopt the technology. The flipside of the coin is that metal 3D-printing requires a large capital investment from the company, skilled labor and expensive feedstock. Current technologies can cost up to $1,000 per pound of produced part which is greatly limiting applications and market potential. The game is on to transform metal 3D-printing into an industrial viable option. Supported by imec.xpand, Fabric8Labs entered the race with a new printing technique called ECAM (electrochemical additive manufacturing) that matches and even exceeds the key 3D-printing deliverables but with a tenfold lower cost of ownership. Co-founders Jeff Herman, CEO and David Pain, CTO explain how ECAM will revolutionize metal additive manufacturing.
The ECAM process.
Taking an electrochemical bath
With a background in manufacturing, Fabric8Labs’ founders noticed that there was no great technology out there for metal 3D-printing. Most state-of-the-art processes use a thermal technique that fuses metal powders together. Right now, this requires machines with complex laser systems, but also the metal powders are very expensive. That, of course, really limits the applications for 3D-printing. Fabric8Labs’ answer to this hurdle is called ECAM or electrochemical additive manufacturing. Inspired by a similar electrochemical deposition technique in the semiconductor industry for making very small structures for MEMS devices, they developed ECAM into a flexible solution for the 3D-printing industry. This technique does not use any thermal processes, lasers or powders, but instead is purely based on electrochemistry. The starting material is an electrolyte bath with metal salts dissolved in solution; the printhead is a micro-electrode array. By selectively activating the electrodes in the preferred pattern, a current passes through the bath and deposits the material.
Activated anode array.
Why electrochemistry beats lasers and powders
One of the main advantages of this technique is the lighter price tag. The cost of technology is lowered in two ways. First, the printer itself is cheaper because the expensive components from a traditional metal 3D-printer, such as the laser, are not present. Secondly, and most importantly, the electrolyte in the ECAM-printer is significantly lower cost compared to metal powders. The consumables are consequently an order of magnitude cheaper than what the competitors are currently offering.
That’s only half the equation. The fact that you’re building parts on an atomic level also comes with an advantage in terms of quality. When fusing metal powders together, you can end up with microvoids, rough finishes and thermal stressing issues. The ECAM-process does not suffer these issues since it builds atom by atom, resulting in fully dense items with very good surface finishes.
Finally, another advantage of this technique over a laser system is that an entire layer is built at once rather than scanning a laser across the build surface which makes it easy to scale. Together with imec, Fabic8Labs is therefore looking into opportunities to develop the printhead for larger and larger sizes. Currently, the printhead – and thus the printing area – is limited to 1 square inch (25 by 25 mm), but that will scale up as the technology progresses into printheads the size of a large monitor or tv. That allows you to produce parts at low-medium volumes or very large pieces. This is simply not possible for the laser systems. They would need to continue adding lasers to get the volumetric building volume to continue to scale. Whereas for the ECAM-technology: the bigger the printhead, the more area you can build in one go.
The scaling roadmap for the ECAM-printer.
Teaming up with imec
The printhead is also the reason that Fabric8Labs got engaged with imec early on. The initial proof-of-concept technology was a crude, low-resolution implementation with large electrodes. It quickly became clear that the semiconductor industry was the way forward to implement the miniaturization. At this point, imec jumped in to help with the development of the micro-electrode array with their design services and expertise. The technology was evaluated in a design study and simulation to make it suitable for the application. In this collaboration the printhead was adapted to use thin film display technology, allowing for the first high-resolution 3D-structures to be printed. Furthermore, imec.xpand led the seed investment round of Fabric8Labs with the participation of a US-based corporate investor. imec.xpand is an independently managed value-add venture capital fund that focuses on hardware-based nanotechnology innovations where imec technology, expertise, network and infrastructure will play a differentiating role.
Going forward, imec will also assist with the unique processing of the thin film technology-based backplanes that makes them chemically resistant and dimensionally stable, as well as assisting with the design of the next-generation printhead. The biggest constraint today is the small building volume of 25x25x75 mm. Consequently, for the moment, only small test specimens are shipped to customers, such as material samples, tensile bars, and smaller form factor parts. With the next-generation printer, which will be deployed next year, actual parts can be printed on a 100-by-100 mm printing area. Looking further in the future, for the third-generation printer, even 300-by-450 mm parts will be possible.
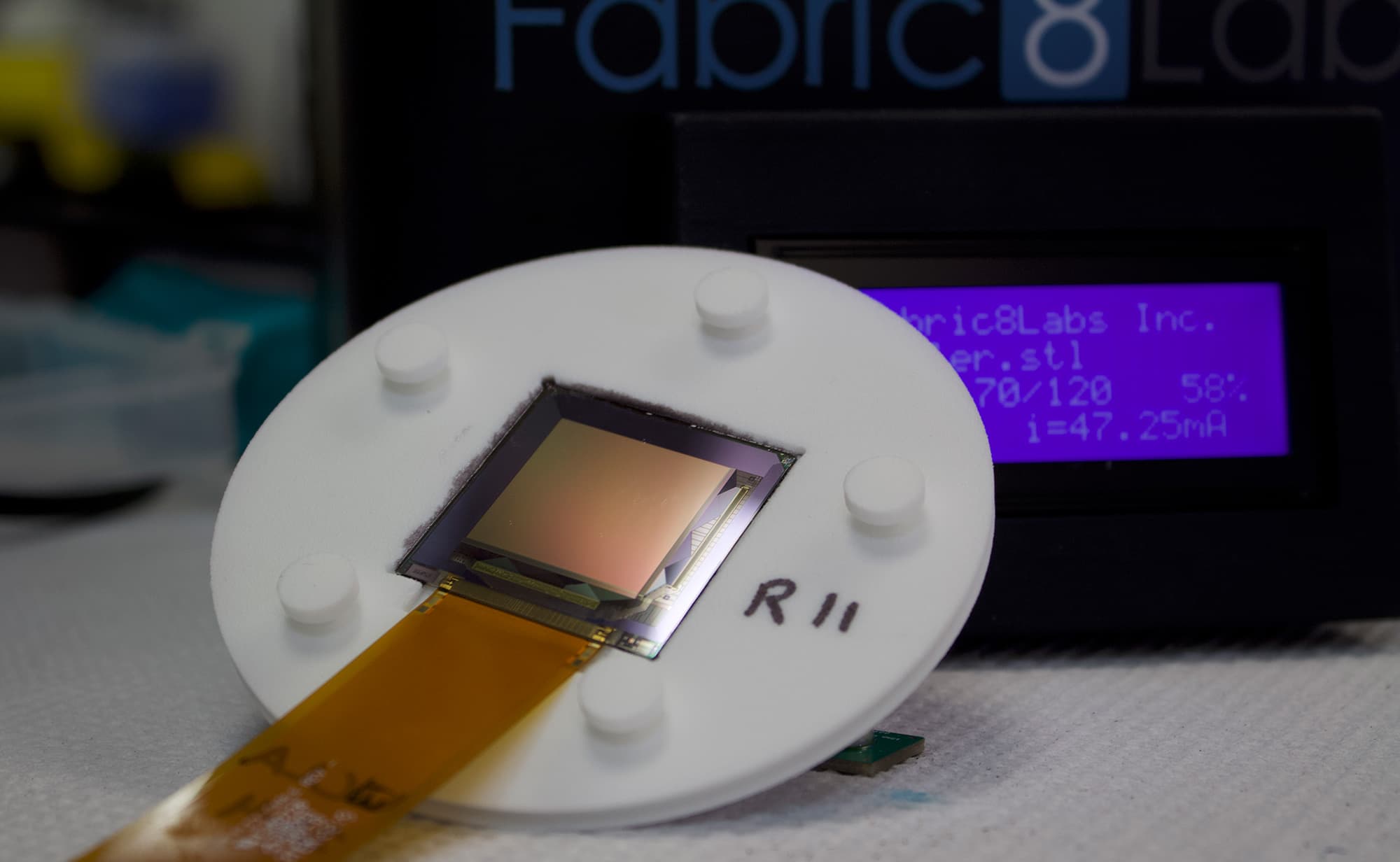
The thin-film technology printhead.
Metals and more materials
The new printing technique doesn’t compromise on resolution or speed, but its biggest drawback is the limited range of materials. ECAM-printing is restricted to materials that can be electroplated, and for the moment there are about 30 to 40 printable materials. There is also a list of materials that don’t work, for example complex alloys that require the control of many different elements. Nevertheless, ECAM enables a whole range of other material options, originating from the fact that the process can utilize all the advancements in the electroplating industry. The low-hanging fruit in this case are copper applications where the technique is a real differentiator. Think about heat exchangers or chip packaging for semiconductor applications that focus on – either thermally or electrically – highly-conductive copper. Other systems struggle with these parts because copper is very difficult to fuse with a laser.
Another opportunity lies in multi-material parts. In the longterm, it will not only be possible to print a different material on the outside and the inside, but also to combine metal and organic material in single parts. As such, everything that can be electroplated can be adapted to the process. There are some plastics that can be electroplated as well as a number of materials that you can add to the bath to co-deposit with the metal. Examples include carbon nanotubes or diamond powders that allow you to take advantage of their unique properties.
The Gen-1 printer.
The future of metal 3D-printing
So, what lies ahead? The main focus for Fabric8Labs now is scaling the printheads to larger sizes. At the same time the development of other materials, such as different nickel alloys, is high on the agenda. They are already doing the chemistry work to develop the chemical baths. The multi-material printing is planned for after that. Looking 5 to 10 years down the road, there are opportunities to make the pixels a lot smaller to allow for the print of MEMs structures and meter size print heads for mass production. This means that it will be possible to go from the current mm-technology to nano-scale printing.
Fabric8Labs: “If we can scale our pixels from the micrometer scale to the nanometer scale, there will be some interesting applications for this technology in the nanoscale in the cleanroom.”
Want to know more?
- Read more about imec.xpand on their website.
- Want to know more about Fabric8Labs: check out their website.
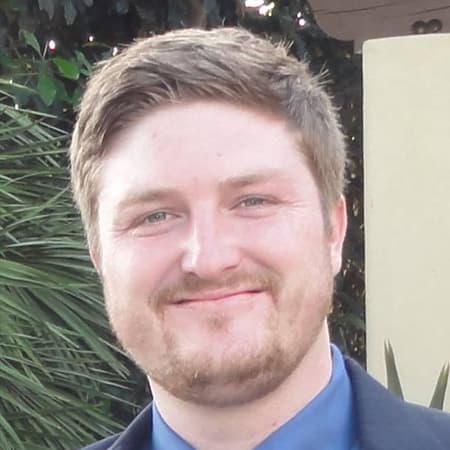
Jeff Herman co-founded Fabric8Labs in 2015 and is responsible for the overall vision and operation of the company. In 2017 Jeff was selected for the Forbes 30 under 30 for his part in developing Fabric8Labs’ patented electrochemical approach to metal additive manufacturing.
Before joining Fabric8Labs, Jeff held leadership positions at several startups including Limelight Health, JSquare, and Scentsa. Jeff holds a Bachelor of Science in Business Administration from California Polytechnic State University, San Luis Obispo.
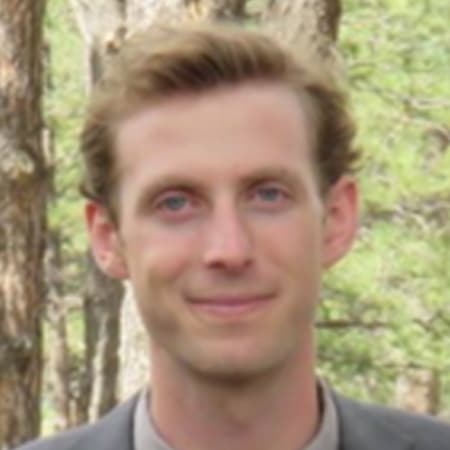
David Pain co-founded Fabric8Labs in 2015 and is responsible for developing the company’s core technology and building the engineering team that has brought the concept to reality. In 2017 David was selected for the Forbes 30 under 30 for his part in developing Fabric8Labs’ patented electrochemical approach to metal additive manufacturing and is named on multiple US, Canadian, and European patents.
Prior to founding Fabric8Labs, David worked in General Atomcs’ Manufacturing Engineering group. David holds a degree in Mechanical Engineering and Technology Entrepreneurship from University of California, Santa Barbara.
Published on:
8 September 2019