Recently, imec announced a major breakthrough in solid-state battery technology. The research center engineered a new solid electrolyte that has an exceptionally high conductivity of up to 10 mS/cm. According to imec’s Dr. Philippe Vereecken, there is even potential to reach 100 mS/cm, paving the way for a whole new generation of batteries for applications covering the spectrum from small portable electronics to electric vehicles and stationary grid storage. To create optimal solutions for these applications, with a higher energy density, faster charging time, longer lifetime, and an improved safety, imec’s researchers are now looking to further improve the innovative electrolytes and integrate them with thick-layered nanoparticle electrodes with innovative functional coatings.
Since the introduction of the rechargeable Li-ion battery in 1991, it has become the technology of choice for portable energy storage. With its available high energy density, it could store enough energy in a small volume to power the surge of portable electronic devices. But more and more, Li-ion technology is also chosen as the preferred solution to drive larger systems such as electric vehicles or stationary home batteries that store renewable energy and balance the smart electricity grid. These applications, however, place new demands on the battery technology that Li-ion cannot always fulfill.
For electric vehicles, e.g. a key consideration is to have batteries with as low a weight and volume as possible. That calls for an even higher energy density than is possible today. Also, the maximum current flow becomes more of an issue: the time to recharge critically depend on how fast energy can flow in and out of the battery. And as we consider economically critical applications such as grid storage and grid balancing, the cost and related high lifetime also become a key consideration.
Today’s Li-ion technology has some room to improve, but not enough to sustain the future requirements for all these applications. So we need innovation: new cathode and anode architectures with higher energy densities and new electrolytes that can deliver the necessary conductivity and that are safer.
Why use solid-state electrolytes?
An essential component of the battery is the electrolyte, the medium through which the Li-ions migrate between the anode and cathode. In today’s batteries, that electrolyte is a liquid. It fills the open spaces inside the porous membrane that is placed between the anode and the cathode. And it also soaks the powder electrodes, completely filling all pores and spaces and providing as much contact as possible between the electrodes and the electrolyte. Crucial for a battery’s properties is a high ion conductivity, i.e. the speed by which the ions can move about the electrolyte (expressed in mS/cm or milli-Siemens per centimeter). The higher that ion conductivity, the faster a battery can charge. And conversely the more power it can release.
Replacing the liquid electrolyte with a solid would allow removing the membrane and placing the electrodes much closer together, making the battery more compact and thus delivering a greater energy density. Until recently, however, the solid-state electrolytes didn’t have the required conductivity. One such electrolyte is LiPON (lithium-phosphate-salt doped with nitrogen), which has an intrinsic conductivity of only 10-7-10-6 S/cm. But that means the electrolyte layer can be no thicker than one micrometer. The only practical application of such solid-state electrolytes is therefore in planar thin-film batteries in which the ions have to travel only a short distance. Such batteries are great for micro-storage, e.g. in combination with energy scavenging for autonomous sensors , but for other applications their capacity is inadequate.
A breakthrough electrolyte
To engineer new solid electrolytes with an ion conductivity that is high enough to drive large-capacity cells, imec’s scientists have been looking towards composite materials. In November last year, a first result was announced: a new way to engineer nanocomposite materials that amplifies the ion conductivity to exceed that of liquid electrolytes.
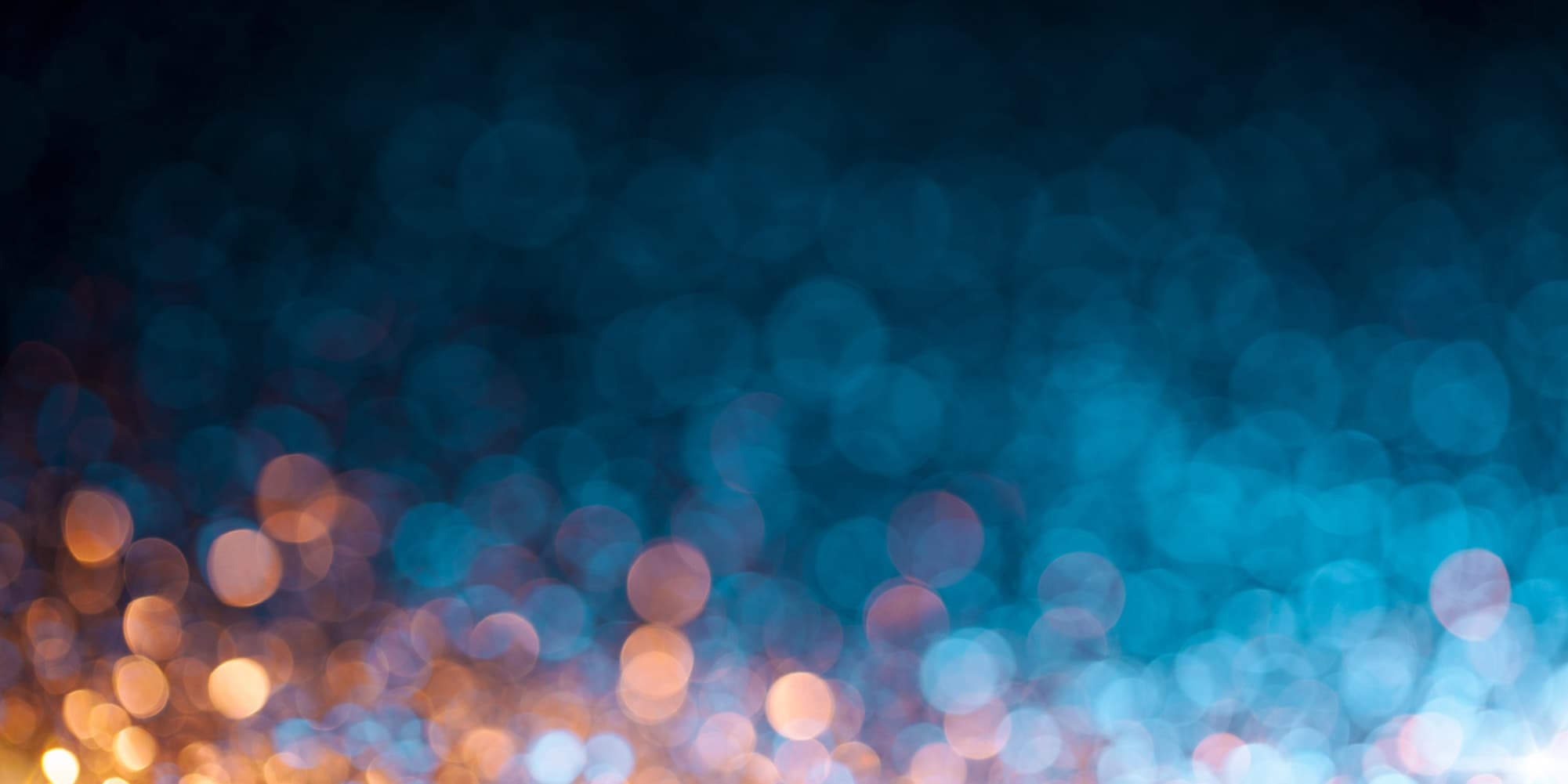
Imec has now set out a path towards novel electrolyte materials targeting 100mS/cm, i.e. tenfold that of liquid electrolytes.
A distinguishing feature of the new solid nanocomposite electrolyte (SCE) is that it is applied as a liquid – via wet chemical coating – and only afterwards is converted into a solid. That way it is perfectly suited to be casted into dense powder electrodes where it fills all cavities and makes maximum contact, just as a liquid electrolyte does. In addition the material retains some elasticity even after solidification, which is critical for batteries as the electrodes expand and contract during charging and discharging. The possibility of wet application of the SCE precursor makes this technology also compatible with current Li-ion battery fabrication processes. This will make it easier for the industry to adopt it compared to materials for which disruptive fabrication processes would have to be put in place.
Imec’s solid electrolyte is a composite of a nanoporous oxide matrix with selected ionic compounds and additives. Unique is that the ionic conductivity of the final nanoengineered product is higher than that of the Li-salt electrolyte without the oxide matrix. That effect is attributed to an enhanced mobility of the Li-ions along the oxide surface. As the material has an extremely large surface area of about 500m2/mL – comparable to an Olympic swimming pool folded into a shot glass – the result is a Li-ion conductivity exceeding 10 mS/cm at room temperature.
With this new material, imec’s engineers have already built a cell prototype using standard available technology for the electrodes: LFP (LiFePO4) for the cathode and LTO for the anode. Compared to a similar cell made with liquid electrolyte, the new cell reached 80% of the capacity at a charging rate of 1 C (h-1). And there is reason to hope for even better results: computations show that the new SCE can in theory be engineered to sustain conductivities of up to 100 mS/cm, which is a target set by imec in its open innovation research program.
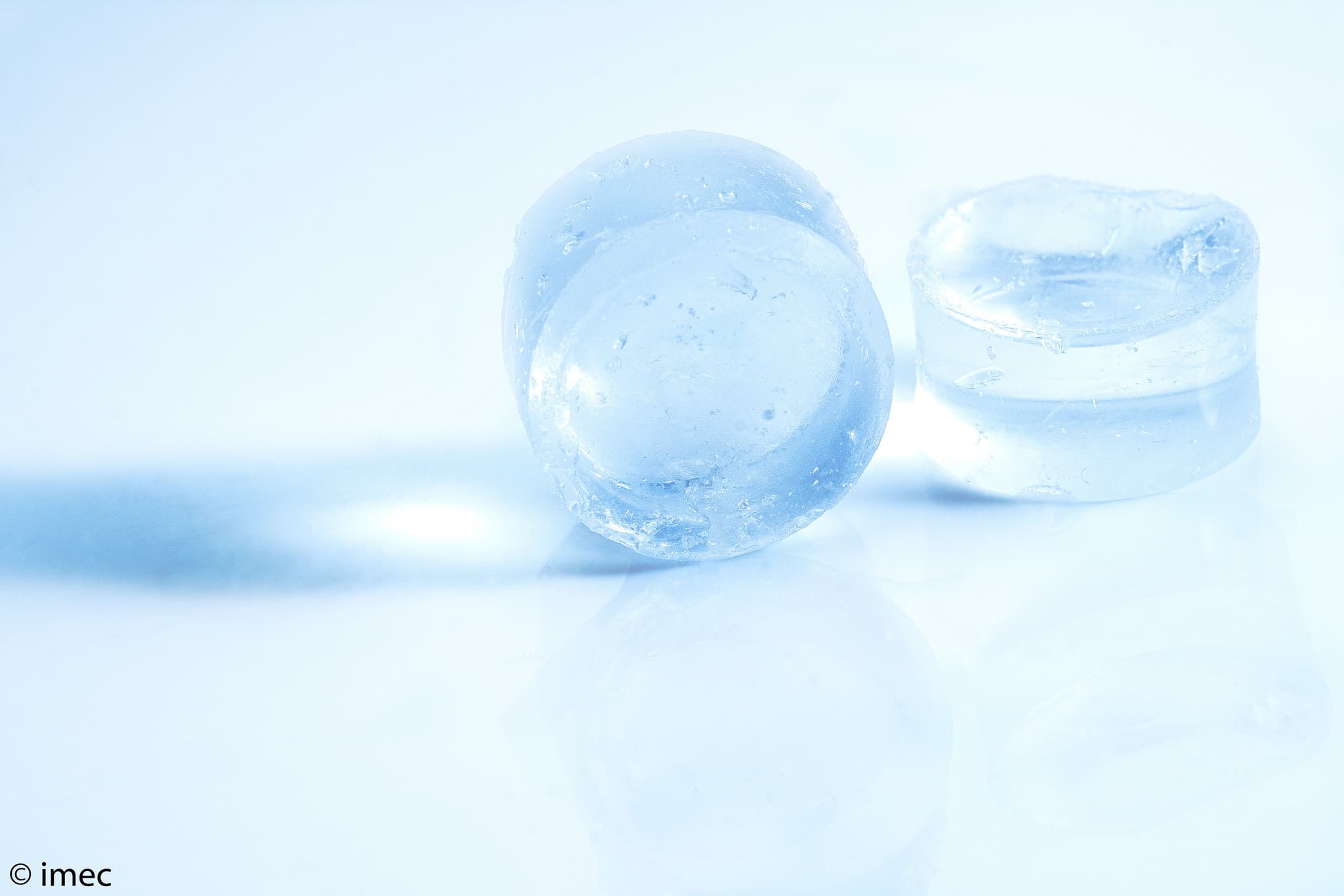
Imec and Panasonic's new electrolyte
Smaller particles, higher energy density
To get at the energy densities required for e.g. electric vehicles with long driving range, more will be needed than new electrolytes. We will also have to engineer the electrodes to contain more active material. The solution seems straightforward: use smaller electrode particles, which can be packed even more densely in the electrodes. As these will have a higher surface contact per volume, this should also improve the power and charging rate of the cell.
But here the issues for improvement are the same as with liquid electrolytes: a greater contact surface also greatly promotes surface reactions and thus material degradation. Therefore, to extend the stability window, imec’s experts work on a solution applying an ultrathin buffer layer to the particles through ALD (atomic layer deposition), another core expertise of imec. These layers should of course be chemically inert and highly conductive, lest they behave as insulators and neutralize the enhanced surface again.
With such a surface passivation, it will become possible to apply smaller particles in the electrode. And because the solid-state electrolyte allows applying thicker electrodes, this also opens the potential for batteries with a higher energy density, considerably exceeding 800 Wh/l (at a charging rate of 2C or more; i.e. a battery is charged in less than 30 minutes).
To extend the energy density even more, towards 1,000 Wh/L and beyond, imec is working on lithium metal anodes. Lithium metal has the highest energy density possible for the anode and is the Holy Grail for rechargeable lithium batteries. But currently it can only be used in primary or non-rechargeable Li-batteries. For rechargeable batteries, the use of metallic lithium may affect the lifetime and reliability of the batteries, as recharging promotes the formation of metal needles that may short the cell Imec researchers believe they can overcome these issues through a combination of a rigid solid-electrolyte component and thin buffer layers at the interfaces.
Joining research efforts
The previous decade progress in battery development has concentrated on electrode materials and improvements in the existing Li-ion technology. More disruptive improvements, such as the move to solid-state electrolytes, require a concerted and sustained research effort. And they also demand looking at the challenge with new eyes and from new angles.
At imec we can leverage our unique expertise in nanomaterials, thin-films and interfaces, expertise gained from decades of semiconductor processing research. An example is the know-how on mesoporous materials for low-k dielectrics in chips. This experience has contributed to the development and testing of the novel nanocomposite electrolyte. Likewise, the extended know-how in thin-film deposition in high-aspect ratios is now used to create innovative coating of battery powder electrodes.
When this endeavor can now be combined with the concerted effort of material and battery suppliers, the road is open to better, safer batteries that will drive the electrified future.
Imec’s development of next-generation batteries is embedded in an open innovation program, in which Panasonic is one of the partners. The research is part of EnergyVille, a research initiative that brings together the expertise of imec, KU Leuven, VITO, and Hasselt University to develop sustainable energy and intelligent energy systems. A next step is to upscale the current innovations in the new state-of-the-art battery lab (including dry room) on the EnergyVille campus.
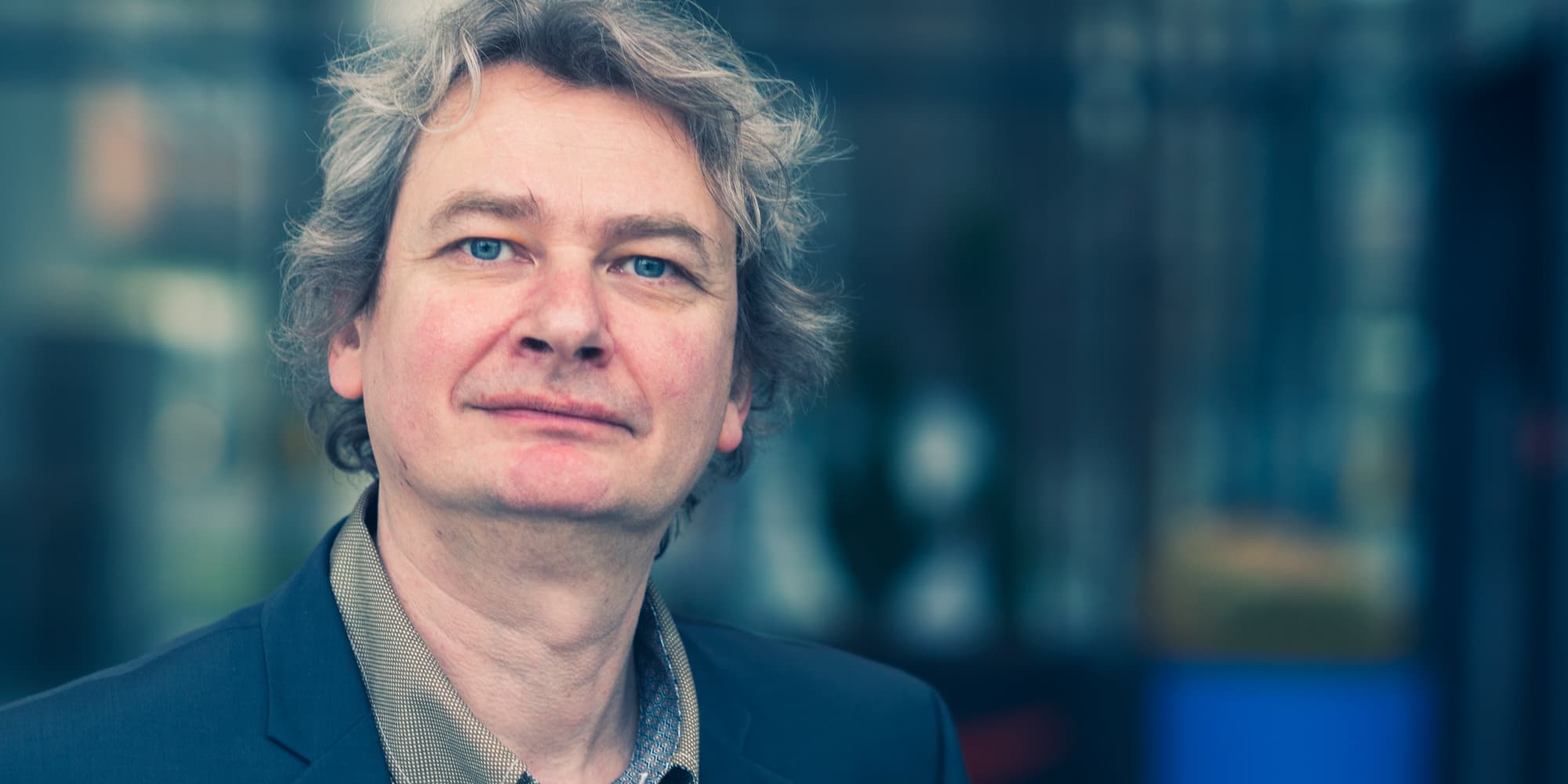
Philippe Vereecken obtained a PhD in physical chemistry in 1998 from Ghent University. After a stay at The Johns Hopkins University as a postdoctoral researcher, he worked at IBM Research (New York) as research staff member (RSM) for several years. In 2005, he joined imec, first in the nanomaterials group. In 2009, he was appointed Associate Professor at the Center for Surface Chemistry and Catalysis, Faculty of Bioscience Engineering, KU Leuven. In 2010, Philippe Vereecken started the energy storage activities at imec. Currently, his work is focused on the development of solid-state Li-ion batteries.
Published on:
1 February 2018